Improving the carbon footprint in all metal-related areas of daily life (e.g. steel construction) is an important step towards achieving the European climate goals. But what does the carbon footprint of steel actually look like? A so-called cradle-to-gate analysis provides reliable data by determining the CO₂ value stream for the respective steel consumer. It looks at both the energy and material efficiency of steel, from production to the finished product, and also takes into account the logistics.
The current results are disappointing: green steel is still a dream of the future. The transformation of the European steel industry to zero-emission production is an expensive and complex process. However, there are already concepts for environmentally friendly and resource-saving production. In the following article, we will take a closer look at what is already possible today and what is still needed to produce sustainable steel.
Green Steel - What does it actually mean?
The term green steel has two meanings:
- strictly speaking, CO₂-neutral steel (zero emission)
- in everyday use, CO₂-reduced steel
What at first glance sounds like a contradiction, makes sense once we consider that we are currently in the middle of a development leap from black to green steel. After all, steel production without any CO₂ emissions is still wishful thinking today, while leading corporations have already set a target of producing exclusively CO₂-neutral steel by 2045.
In terms of specific measures, this means a total elimination of blast furnaces powered by fossil fuels, as well as supplying energy-intensive manufacturing exclusively with energy from renewable sources. Manufacturers are currently working on noticeably reducing the CO₂ footprint of their products. What sounds rather easy is a complex issue in reality and the road to the green future of steel is still long.
How sustainable Steel becomes reality
There are now practical processes that allow emission-reduced steel production and so pave the way for the long journey toward CO₂ neutrality.
Direct reduction with hydrogen
Hydrogen is an essential component in the production of green steel, and hydrogen-based direct reduction is a practical technology for avoiding CO₂ emissions. In this process, gaseous hydrogen flows around iron ores in a shaft furnace and reduces them when the reaction energy is sufficient. This process takes place at lower temperatures than in the blast furnace and produces what is known as hot-brick iron (HBI) instead of liquid pig iron. This is melted into steel in electric arc furnaces or smelting furnaces.
As long as the hydrogen, which is energy-intensive and costly to produce, is not yet available in sufficient quantities, natural gas can also be used for direct reduction. This method saves up to two thirds of CO₂ emissions because methane, the main component of natural gas, is a hydrogen-rich gas.
Scrap-based electric steel
Electric steel production based on scrap (secondary steel production) already allows a significant reduction in CO₂ emissions. In this process, scrap is melted into new steel in an electric arc furnace using electricity. As steel can be recycled again and again without any loss of quality, this process saves resources and at the same time helps reduce greenhouse gas emissions, especially if electricity from renewable sources is used. However, due to the inherently limited amount of steel scrap, this production method cannot be expanded at will. Nor does the process offer the full spectrum of material qualities of an integrated steel mill.
4 Examples of how steel can be sustainable
Due to its material properties, climate- and resource-friendly handling of steel as a raw material and its integration into a sustainable circular economy is already feasible today. The following 4 reasons speak in favor of this:
- High proportion of scrap recycling:
According to a recent statistical report by the German Steel Federation, 84 percent of the steel ever produced worldwide is still in use due to its durability and recycling. According to the report, 35.7 million metric tons of crude steel were produced in Germany in 2020, using 15.8 million metric tons of scrap steel. - Efficient use of materials through sustainable processes (roll forming):
Roll forming produces very little steel scrap compared to other processes and after reduction to 800 millimeter long pieces, the scrap can be directly reused in steel mills or forges as high-quality, unmixed scrap. - Recyclability of steel:
Steel is 100 percent recyclable and without loss of quality if it’s collected by type during recycling. (Mixing with other materials can reduce the quality during remelting and lower the grade of the steel). Through repeated processing in secondary steel production, scrap steel contributes significantly to CO₂ reduction in the life cycle of a product. According to the statistical report of the German Steel Association, recycling saves more than 1.5 tons of iron ore and more than 0.65 tons of coal per ton of steel produced. - CO₂-reduced logistics:
Steel is already transported by rail in many cases and thus makes a major contribution to reducing CO₂ emissions in the logistics sector. Whereas an average truck emits 86.7 g of greenhouse gas emissions per ton of freight volume per kilometer, the equivalent amount is only 4.1 g for rail transport. A kilometer of transport by rail is therefore over 21 times more environmentally friendly than by road.
What’s holding back sustainable Steel Production?
While we know that steel as a finished material is an extremely sustainable material we also know that there is significant scope for improvement over traditional production methods. Depending on the manufacturing process and feedstock material, there are in some cases very adverse effects on the climate balance.
Integrated blast furnace route (BOF)
In the blast furnace process, iron ore and reducing agents such as coking coal are used to produce liquid pig iron, which is then transformed in the steel mill with any desired alloy. At 2.1 metric tons of CO₂ per ton of steel, this process is responsible for the largest share of climate-damaging emissions. The coal required for production can be replaced to a certain extent by hydrogen in this process. This offsets the negative effects, at least to some extent. However, hydrogen produced from renewable energy is currently scarcely available.
Electric Arc Furnace (EAF)
The Electric Arc Furnace (EAF) route is a steel production method that offers significant emissions reductions. It involves using up to 100% steel scrap as the main feedstock in an electric arc furnace, resulting in direct emissions of 0.1 to 0.3 tons of CO₂ per ton of steel. However, additional effort is required, as the steel scrap used for production first has to be sorted and different material grades separated from one another. Consequently, it is not possible to produce the entire range of higher-alloy materials through the electric steel route. Another drawback is the relatively high electricity requirement for the process. However, at present, manufacturers still have limited access to electricity from renewable sources. Despite these challenges, the EAF route remains a significant contributor to steel production in the EU, accounting for just over 40% of the total output.
Sustainability made possible by Roll Forming
Roll forming enables both standard and custom profiles to be produced with high precision from coiled steel strips. For this purpose, the strip is cut to the correct width and shaped at room temperature on the roll forming line to meet the respective requirements. Thanks to this process, roll forming is a convincing solution in terms of sustainability:
- Reduction of process steps
Through the combination of several process steps the need for classic handicraft work such as sawing, punching or filing is obsolete. - Energy efficiency
Roll forming takes place at normal room temperature without additional energy requirements. - High material utilization
Due to the nature of the process, a very high proportion of the raw material is processed during roll forming. - Reduction of material thickness
Roll forming allows the use of high-strength and micro alloyed steel grades, thus reducing the necessary material thickness and lowering the weight of the end product.
Future Prospects for Green Steel
The technical possibilities for producing climate-friendly steel are already available today and will continue to be driven forward by leading manufacturers in the future. The aim is to gradually replace fuels from fossil sources with hydrogen and electricity from renewable energies and achieve total CO₂-neutral steel production by 2045 at the latest. In Sweden, for example, the greenest steel mill in Europe is planned - a plant in which the energy for the strongly CO₂-reduced electric arc process comes from hydropower.
Nevertheless, it is also clear that the effort required to produce green steel with the aid of modern technologies is higher than with conventional processes, and so are the costs. After all, a changeover not only means the introduction of new production processes, but also the integration of a completely new manufacturing process into a steel manufacturer's existing process chain.
Another factor that should not be overlooked in the sustainability discussion is location. Up to now, proximity to the customer and the logistical availability of raw materials were the primary location arguments. In the future, it will be the availability of renewable energy, especially green electricity and green-generated hydrogen. While the automotive industry, for example, has expressed great interest in climate-neutral steel, it is only prepared to share the necessary investment to a limited extent.
The Ukraine crisis in particular shows how quickly many companies put their good intentions with regard to green steel on the strategic sidelines as soon as money is at stake.
No sustainable Steel without binding Regulations
How quickly the urgently needed switch to green steel will take place is in the hands of processors and politicians. The former will have to ask themselves which steel they want to demand and trade on the market in the future: comparatively cheap CO₂ guzzlers or products from CO₂-reduced production. Politicians, in turn, must take a firm stand against climate-damaging manufacturing processes by implementing effective tariffs (CBAM) and support those players who are actively working for a green future for steel production.
Bottom line: Our contribution to sustainable steel
At Welser, we are committed to sustainable production practices by sourcing our materials from local suppliers who share our views and climate goals. In addition, we take a holistic approach to reducing our carbon footprint. We distribute steel by rail, process it in a resource-saving way using roll forming, and recycle the small amount of scrap generated in the process in a closed-loop manner for reuse in the steel mill. In addition, we also utilize solar energy in our operations. For example, at our location in Germany, we are building a 200-meter tall state-of-the-art wind turbine to further enhance our use of renewable energy sources.
Finally, it is always our pleasure to share our many years of expertise in sustainable steel and to provide customers and project partners with advice and support for realizing their projects in the most climate-friendly way possible.
Read more
Similar articles
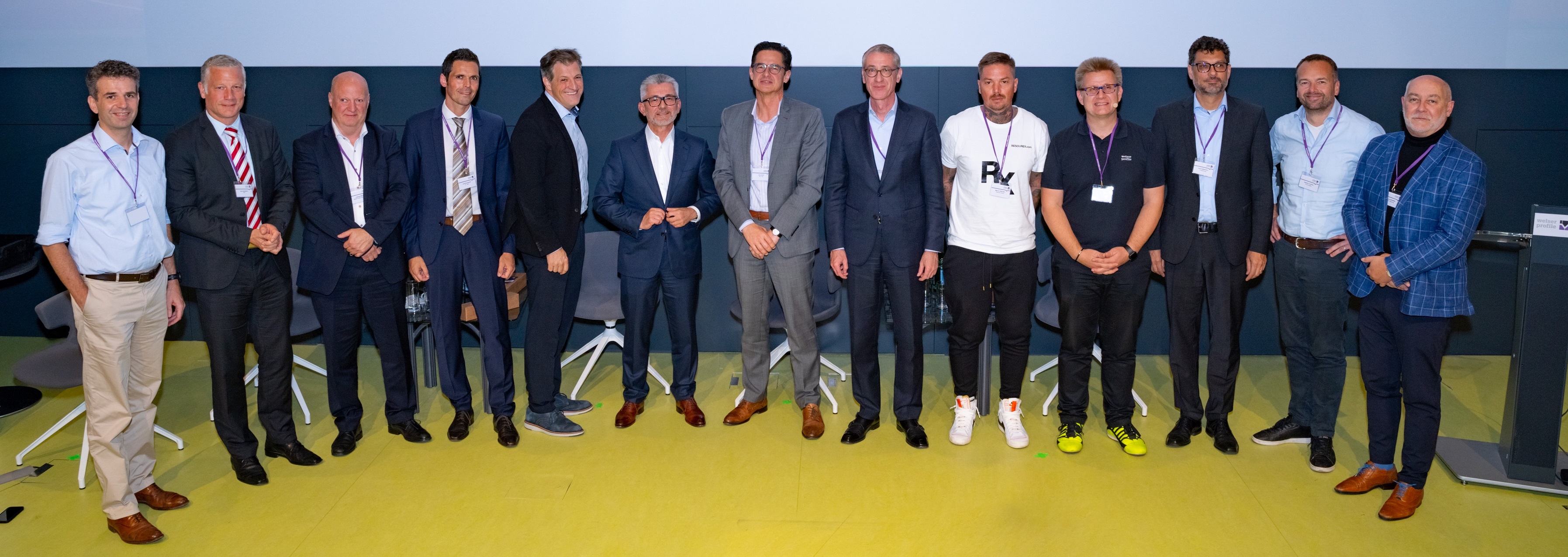
Steel Day 2022: Digitalization, Automation, Decarbonization
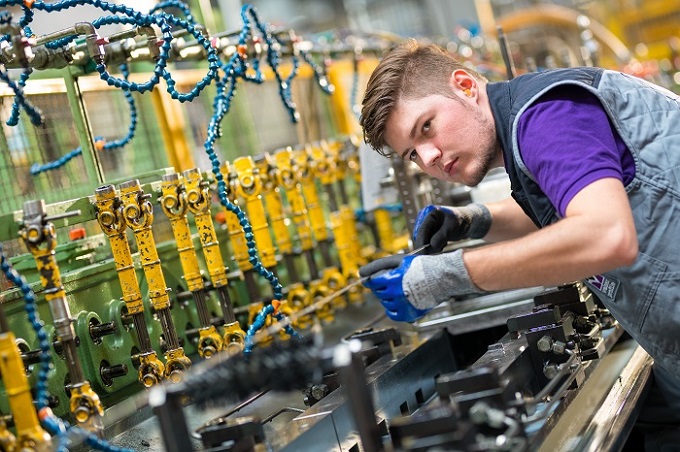
Green Steel in Roll Forming – The same thing, only greener?
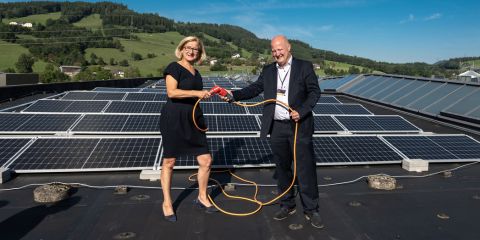