The Future of Steel in 2024: A Turning Point for the European Steel Industry
Is there a future for the European steel industry? This weighty question was all but ubiquitous in Gresten, Lower Austria, on Tuesday, September 10. For one day, the small market town had become the undisputed center of the steel industry. Important industry representatives and leading experts accepted CEO Thomas Welser's invitation to discuss current developments, challenges and visions for the future at Welser Profile's Future of Steel event - also known as "Steel Day". But the main focus of this day - as the host emphasized in his rousing opening statement - was to promote cohesion within the industry.
With this in mind, Jörn Miklas, Vice President of Steel Management at Welser Profile, and Daniel Killinger, Director of Business Strategic Accounts, were fully prepared to lead a high-caliber lecture program and equally engaging panel discussions. So how can the steel industry succeed in reducing its environmental impact while maintaining its competitiveness? In this review, we’ll look at some exciting insights and new perspectives that will help answer this all-important question.
The Transformation of the European Steel Industry
Can our industry stay competitive? Blastr CEO Mark Bula has a clear opinion on this: If the European steel industry is to continue to compete globally, it urgently needs to be transformed. He sees a particular problem in the dependence on iron ore imports from the BRICS countries and the dependence of domestic industries. Without massive investments, he foresees that Europe would eventually cease to play a relevant role in steel production.
Another key factor for Bula is the (currently) inadequate financial support for large-scale projects to transform steel production. Here, the CO₂-intensive blast furnace route needs to be replaced by more sustainable processes in electric steel furnaces. The USA is currently way ahead of us on this. 85 percent of the steel produced there already comes from electric steel furnaces.
Mark Vance from Steel Technologies shares this view. The American expert gave his audience a clear overview of why green steel production in the USA is already much further ahead than in Europe, thanks to the focus on electric steel furnaces and steel scrap. But even across the Atlantic, Vance still sees many challenges for the steel industry on the road to decarbonization. One particular sticking point is that the quality of the steel decreases each time it’s recycled, to the point where it eventually becomes unviable for certain uses.
Using Steelcoin to combat Price Risk: Steel Trading meets Blockchain
After oil, steel is one of the most traded materials in the world. And yet, until now, it’s been almost impossible to invest in the performance of steel. With Steelcoin this is set to change. Frankstahl CEO and Steelcoin inventor Marcel Javor explained his vision in the first presentation of the day.
Steelcoin…
- is a regulated security under European law;
- is linked to the price development of specific steel products;
- is issued in 30 European countries (with 500 million potential investors);
- based on the Ethereum blockchain;
- makes steel accessible as an investment for everyone;
- is traded on www.steelcoin.com, on trading platforms such as Bitpanda, and also as an ETP security at banks or online brokers.
And what is particularly interesting for steel traders is that Steelcoin could also be a convincing hedging instrument, as Javor emphasized. This would make it possible to calculate long-term projects without price risk.
Sustainability through Longevity and Circular Models
An alternative approach for sustainability in the steel industry was presented by Carl Swoboda and Herbert Sikovc using the example of the Wuppermann Group. The company's strategy: creating longer-lasting products with corrosion protection that uses a special zinc-magnesium alloy. This not only saves resources, but also extends the durability of the products treated with it. A pragmatic approach that Chinese manufacturers are now also pursuing, and one which could be a good alternative to solely investing in green steel.
ZINQ has also taken a similar path, as ZINQ Managing Director Lars Baumgürtel explained in his presentation. The leading developer of surface technology is convinced that a circular economy is the key to greater sustainability and the maximization of scarce resources. To this end, the company is working with new technologies and coatings that use 80 % less zinc and can make steel last for over 100 years.
Transparent Sustainability with Environmental Product Declarations (EPD)
Therese Daxner, founder and managing director of Daxner & Merl, supports companies in measuring the impact of their products on the environment and proving this with the help of Environmental Product Declarations (EPD). Based on an independently prepared life cycle assessment, this provides a sound basis for decision-making for companies, as well as objective information for customers and partners, Daxner explained.
These include two aspects that are essential for the steel industry:
- Determining the environmental impact of a product requires looking at the entire value chain - from raw material extraction to production, transport and application, through to recycling.
- It is important to consider not only the CO₂ footprint, but also other environmental impacts in order to avoid a so-called “carbon tunnel vision”.
CO₂-Reduced Steel Production in Practice
Several speakers at Steel Day demonstrated that CO₂-reduced steel production is more than just a theoretical concept.
In his presentation, Eike Brünger, Member of the Management Board at Salzgitter Flachstahl GmbH, was able to demonstrate how the group is carrying out a comprehensive transformation with its SALCOS initiative (Salzgitter Low CO₂ Steelmaking) and aims to reduce CO₂ emissions by over 95 % by 2033. This is to be achieved, among other things, by using hydrogen as a reducing agent in blast furnaces.
However, these factors will also play an essential role in a fully successful transformation:
- the availability of green hydrogen;
- political support in the form of emission certificates and investment incentives;
- the willingness of consumers to pay higher prices for green steel.
Lukas Preuler from Primetals Technologies then presented some innovative technologies for reducing CO₂ emissions in the production of hot-rolled steel. The company's new Arvedi ESP (Endless Strip Production) line, which combines the casting and rolling processes, attracted particular attention. Like the previous speaker, however, Preuler also pointed out that the transition to clean production comes with a price that ultimately has to be accepted by consumers.
But green steel isn’t just a topic for the big steel companies. With its ARVZERO technology, the Italian Arvedi Group shows that smaller manufacturers are also making big steps. As Alessandro Geroldi explained, his company's products are a circular steel that comes from recycled scrap and promises "zero waste". More than 90 % of the waste generated in the production process is recycled and climate-damaging gases according to Scope 1 and Scope 2 are drastically reduced. But the core problem here too: considerable resistance from all players throughout the supply chain (Scope 3), and lack of willingness to pay higher prices for sustainable products.
CO₂ Compensation: A sensible step in the right direction or just a drop in the bucket?
Jodok Batlogg from Tree.ly spoke about the precarious situation of European forests due to extreme weather events such as gusts of wind, prolonged dry periods or high rainfall, as well as the urgent need for CO₂ compensation through reforestation projects. However, compensation measures alone are not a solution to climate change. The expert called for a much stronger focus on green energy in order to achieve global climate goals.
What companies can do:
- Transparent accounting of their greenhouse gas emissions
- Reducing greenhouse gas emissions in line with EU climate targets
- Pricing of CO₂ emissions in their products
- Public commitment to more climate protection
Opportunities and Challenges with Artificial Intelligence
Artificial intelligence is significantly changing the way we live and work. The impact it’ll have on the steel industry was a recurring theme at this year’s Steel Day. In a high-profile panel discussion,
- Sarah Buchner (Trunk Tools, Inc),
- Ali Nikrang (AI Researcher, Ars Electronica Futurelab),
- Stefan Rotter (Data Analytics, Supply Chain Planning, Welser Profile),
- Christian Wallmann (AI Expert, Data Scientist, Welser Profile) and
- Thomas Welser (CEO Welser Profile)
all laid out the challenges and opportunities of using artificial intelligence.
Dabei ging es nicht nur um technologische Aspekte, sondern auch um ethische Fragen und die signifikanten Unterschiede zwischen den USA und Europa im Umgang mit Künstlicher Intelligenz.
The discussion not only covered the technological aspects, but delved into the ethical issues and the significant differences between the US and Europe in dealing with AI.
While new technologies are assessed and comprehensively regulated in the EU, including with regard to potential risks, the pace of transformation in America is primarily determined by profit interests. For Sarah Buchner, this is a key aspect of why Europe is falling further and further behind when it comes to necessary innovations.
What about at Welser Profile? Christian Wallmann emphasized the importance of optimization processes using artificial intelligence, which are already showing great success through chatbots and in predictive maintenance. And Stefan Rotter offered impressive insights into the construction of a data stack that covers the entire supply chain and makes it significantly more efficient - from the supply to the delivery of the products.
Geopolitical Challenges for the Steel Industry
The war in Ukraine, Brexit, and the trade war between the USA and China have slowed down globalization and imposed new challenges on the European steel industry. Gunther Reimoser from EY concluded the varied lecture program with this assessment of global developments. His recommendation: The steel industry must adapt its strategies to the new geopolitical realities.
To achieve this, decision-makers should take the following steps:
- Incorporating geopolitical considerations into business models and strategies
- Increasing the resilience of global supply chains
- Adapting their sustainability strategies to geopolitical realities
And the geopolitical dimension was also omnipresent in the final round of discussions. Is China a threat to Europe's steel industry? And how can we assert ourselves on the global market? The fact is that China is investing heavily in expanding its production capacity for green steel, while Europe lacks a clear vision and is falling further and further behind in the implementation of sustainable steel production. It will take great efforts to make the European steel industry fit for the challenges of the future.
Conclusion: A Sustainable Future is Achievable Through Joint Action
At the end of an inspiring day full of intelligent insights and plenty of food for thought from a wide variety of perspectives, one thing became clear: the switch to more sustainable steel production is urgently needed to secure jobs and reduce CO₂ emissions. A clear strategy and ambitious implementation are needed to continue to compete internationally.
Europe's steel industry only has a future if all its stakeholders pull together. Decisive factors will be technological innovations, new political frameworks, and, above all, the willingness of consumers to pay higher prices for green products.
Read more
Similar articles
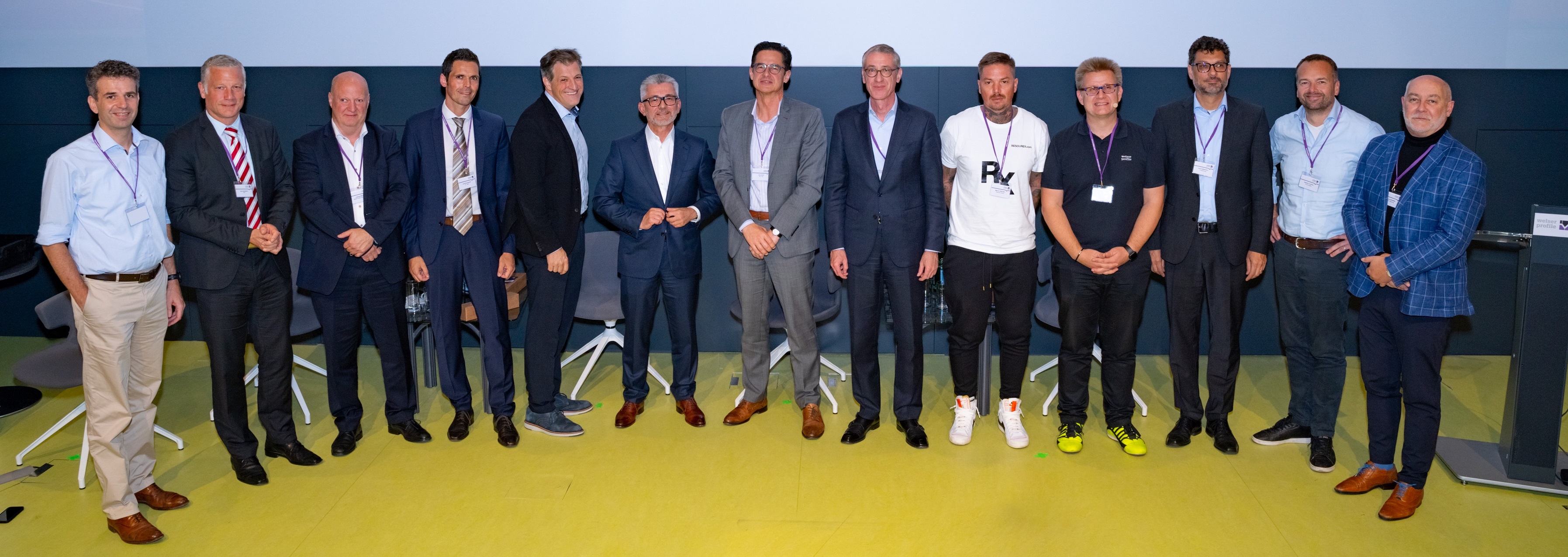
Steel Day 2022: Digitalization, Automation, Decarbonization
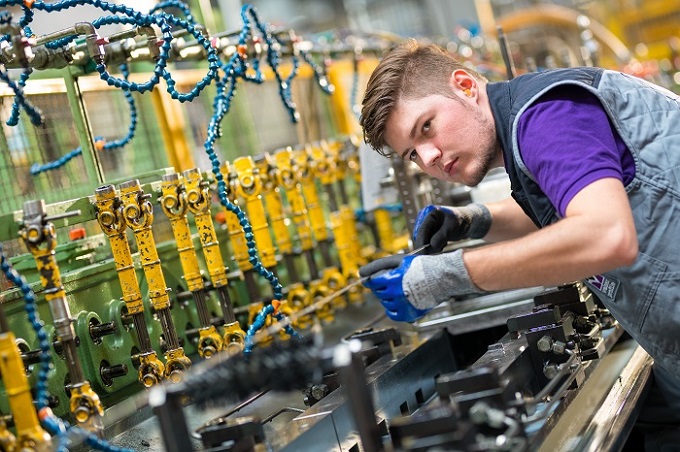
Green Steel in Roll Forming – The same thing, only greener?
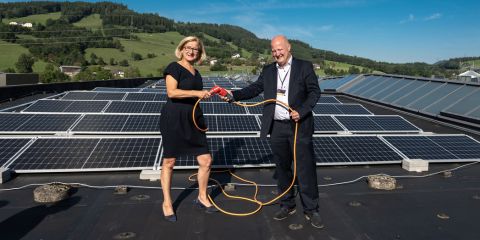