Agri-PV: Making Green Energy greener with Steel Substructures
Photovoltaic systems play a key role in the production of sustainable energy by producing low-cost electricity without harmful CO2 emissions. In order to achieve national climate and energy targets, the Renewable Energy Sources Expansion Act (EAG) believes we need to achieve a massive expansion of photovoltaics by 11 terawatt hours (TWh) by the end of this decade. And according to a study by Austria's energy industry, just relying on the solar potential on buildings won’t be enough.
Accordingly, the majority of the photovoltaic power sources would need to be set up in larger open spaces, and Agrivoltaics (Agri-PV) offers a proven, efficient and fully operational solution. In the following article, we’ll take a closer look at this exciting technology and also take a close look at the necessary substructure.
Agri-PV: Making more Use of each Square Meter
When we talk about Agri-PV, we’re referring to a concept in which land areas are used both for agricultural production and for generating electricity using photovoltaics. This dual use brings more efficiency per square meter by conveniently combining power generation with food production. This is made possible by positioning of the photovoltaic modules a few meters above the ground.
It should be noted, however, that agri-PV currently provides a slightly lower energy output than conventional photovoltaic systems calculated on the same land area. A serious calculation of the return on investment (ROI) should always take into account the yields from agricultural production, i.e. include photovoltaics and photosynthesis equally to get the whole picture.
Practical Dual Use
In addition to their main task as an electricity supplier, the solar modules also make ideal weather protection due to their construction. They shield plants from hail, provide cooling shade, and make planting locations more resilient overall. Another advantage: the reduced solar radiation due to the photovoltaic structure reduces the water consumption of the arable land, protecting the soil from drying out.
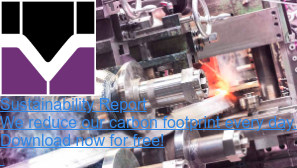
Technology with a Future
The pioneering development of agri-PV can now be found in practically all countries and has developed a remarkable growth dynamic in recent years. From almost 5 megawatts peak (MWp) in 2012, the capacity has increased to approximately 25 gigawatts peak (GWp) in 2024. To put this in context: A typical nuclear power plant usually has an electrical output of 1 GW and supplies electricity for 3 million households. So using Agri-PV as a replacement for traditional energy suppliers is definitely within the scope of what’s possible, but it can only succeed if the appropriate technologies are used extensively across the board.
Agri-PV Key Facts
Quick Look: The most important advantages and challenges of generating energy with Agri-PV at a glance:
Advantages of Agri-PV
- able to utilize huge areas
- cheaper than small PV roof systems
- additional benefits for agriculture e.g. by protecting against hail, frost and drought damage
Challenges of Agri-PV
- reliable forecasts of agricultural yields
- optimization of the plant design with regard to agricultural management
- securing the main agricultural use for Agri-PV along with animal husbandry
- bureaucratic hurdles: the official approval phase currently lasts 2 to 3 years (regional planning, zoning, etc.)
The Right Substructure: A Look under the Hood
Agri-PV systems allow for the generation of electricity and the cultivation of agricultural land at the same time. Accordingly, the solar cells need a substructure that is optimally adapted to each of these respective functions. The goal here is making the best use of the land and having the lowest possible CO2 footprint with the entire system. With this in mind, a number of important questions need to be taken into account when designing the right substructure:
- What weather conditions is the substructure exposed to in the region where it’s to be installed?
- Do the PV modules only serve to generate electricity or do they fulfill other functions (e.g. protecting the cultivated area from hail, letting in more sunlight)?
- How does a certain fruit or plant species react to construction and shade?
- Does a vertical, static system meet all requirements, or is a tracking system necessary that can be flexibly aligned to the position of the sun?
- Which material best ensures the stability of the system?
- Will the foundation allow for the system to be dismantled later on without leaving any residue, protecting the integrity of valuable farmland?
- Which agricultural tools/machine will be used for farming the land?
- Which crop rotations are possible within the structure of the system?
The Right Material: 7 good Reasons to use Roll Formed Steel Profiles
When it comes to choosing the right material for the substructure of the Agri-PV system, roll formed steel profiles are miles ahead of other materials, for 7 good reasons:
- Longevity:
Steel stands for durability in all wind and weather. Structures made of steel are characterized by the fact that they withstand extreme environmental stress over many years. - Stability:
Due to the required construction height of the PV substructures, steel fulfills the necessary requirements with the least amount of material. It’s strong enough to carry heavy snow loads, for example, while at the same time being flexible enough not to buckle under the load. - Climate friendly:
The production of aluminum is much more CO2 emission intensive than that of steel. This gives steel a major advantage for the construction of a system that’s intended to contribute to the reduction of CO2 emissions in general. - Material friendly:
The high load-bearing capacity of the steel allows for the slimmest possible substructure and, given the size of the Agri-PV systems, relatively minimal use of materials. - Cost-Efficient and Scalable:
Once the rollers and tools required for the production of a roll- formed profile have been designed and manufactured, the production process can be repeated as often as you like. A higher demand is thus covered at low cost and production capacities can be flexibly expanded. - Individual Production:
In roll forming, several process steps are combined into one. A thin strip of sheet metal is formed from the outset to incorporate the individual requirements. This simplifies the production of the diverse substructure variants of Agri-PV systems. - Conservation of Resources:
Due to the special manufacturing process, the production of roll-formed profiles also saves raw material waste. This effect can be maximized by precise and sustainable advance planning.
The Right Partner: Green Steel for Photovoltaics with Welser Profile
As a local specialist for made-to-measure roll-formed profiles, Welser Profile is exactly the right partner for the design and manufacture of substructure for Agri-PV systems. Our customer advisors and technicians accompany project partners with their comprehensive know-how on roll forming and help to work out a viable and ideal solution. With our production capacities, we can deliver the substructure for a long-lasting photovoltaic field of 5 ha or 4 MW in a production time of just three to four days.
In addition, we’re happy to bring our industry expertise to the approval phase of PV projects and help make an additional contribution to the expansion of clean energy sources. Just one of the many examples of our work on argrivoltaics can be seen in action in Pöchlarn, Lower Austria, where the prototype of an agri-PV system with Welser Profile technology is already set up.
Advantages to working with Welser Profile
The production of made to measure substructure for Agri-PV systems is of course carried out with the same quality principles that have inspired new customers and long-standing project partners to work with Welser Profile over and over again.
We work efficiently:
Customers receive all manufacturing and finishing processes from a single source and with a production volume of more than 200,000 running meters, the best price-performance ratio in the industry.
We work with your ideas:
We don't just process an order, we make a product roll-formable and optimize it by adding new functions. In this way, we actively contribute to the further development of a profile and the creation of completely new products, while saving additional costs, speeding up installations and improving system features.
We offer active support:
Our sales engineers work with customers directly on site to jointly develop concepts and solutions.
Conclusion: More Commitment to Green Energy is needed
With Agri-PV systems, we have an effective and ready-to-use technology for the production of green energy in large quantities, with the added bonus of keeping the required land available for other uses. Suitable open spaces could be equipped with agri-PV systems in just a few days/weeks, but the relevant permits often take several years to clear. This makes it all the more important to remain persistent and to work to accelerate the process of a full sustainable energy transition.
Read more
Similar articles
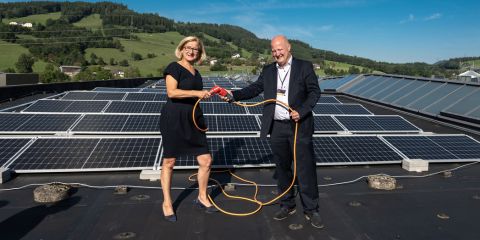
Photovoltaics: Green Steel for Green Energy
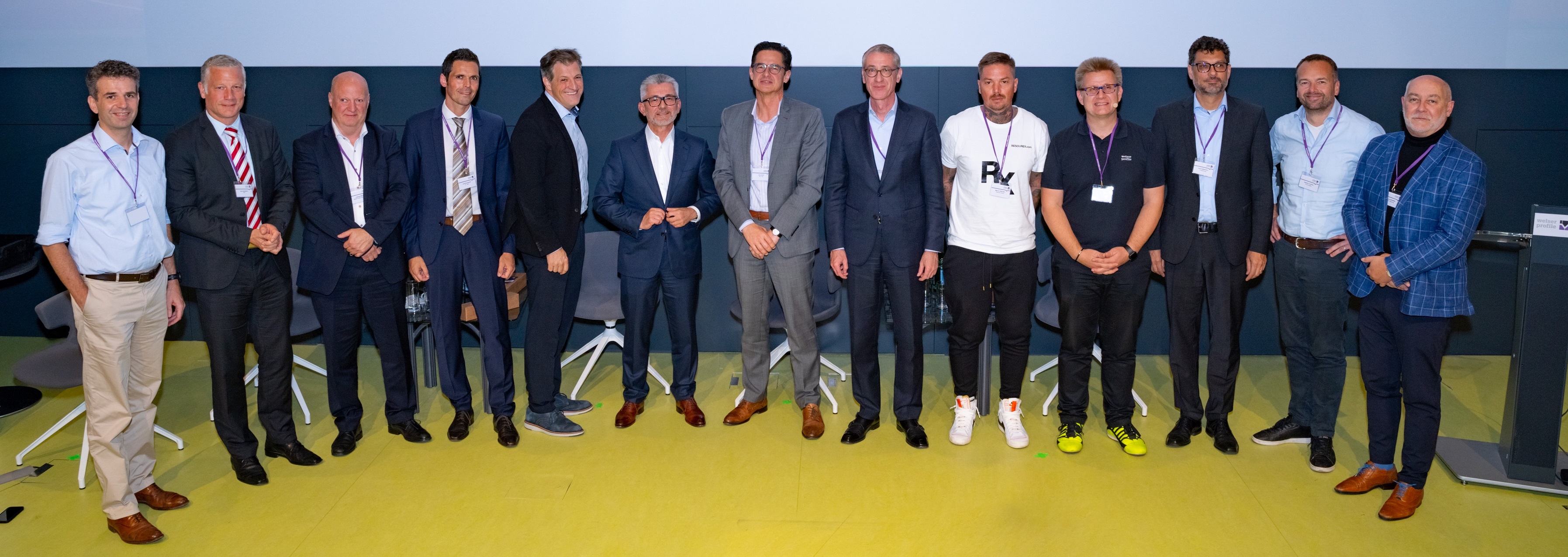
Steel Day 2022: Digitalization, Automation, Decarbonization
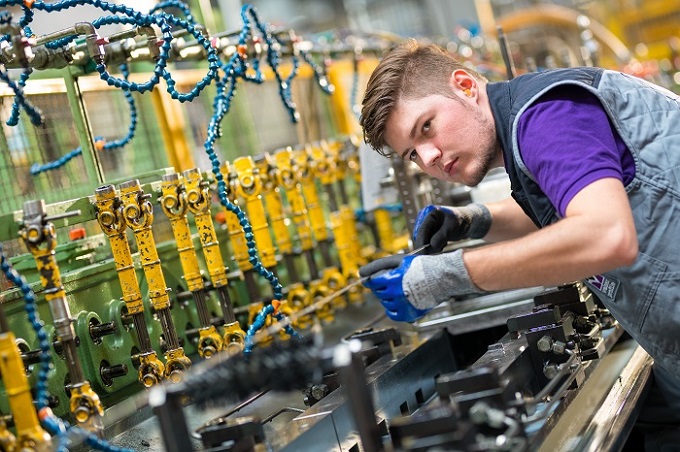