Imagine one of those old-fashioned, hand-operated wooden clothes washers - the kind where laundry was squeezed in between two wooden rollers to wring it out. That’s basically what the rollers look like in the roll forming process. Except that instead of wooden rollers, you have shaped and hardened steel rollers. And now imagine several dozen pairs of these rollers in a row, and instead of the dirty laundry, a really long metal strip is fed through and formed a bit more by each pair of rollers until the desired cross-sectional shape emerges at the very end. This manufacturing process is what we’re talking about when we refer to "Roll Forming" or "Roll Profiling", and it takes place at room temperature.
A long, perfectly formed steel profile of up to 27 meters in length can be cut into manageable pieces at the end for ease of transport and, depending on the profile design, even mounted immediately after delivery, eg. onto a car chassis. Read on to learn exactly how the modern production process of “roll forming” works, what potential it might have for you, and where its limitations lie.
What Roll Forming is
Roll forming is a process used for shaping metals such as steel, stainless steel and solid non-ferrous metals such as nickel, titanium and copper. You might also hear this process referred to as roll profiling or cold rolling. Coils of metal strips are used as the starting material. These are then wound into a coil and fed through modularly arranged rollers in order to create precise, complex cross-sections.
These custom profiles can be (re)produced in large lengths consistently, and with high quality. Additionally, since features such as holes, slots or embossing can be easily added during the forming process, roll forming is considered a highly cost-effective way to produce robust, multi-functional shapes in large quantities. Roll forming is a popular alternative to aluminum extrusion when the material properties of steels are required, or where adding the features into the aluminum profile is a costly secondary process.
How Roll Forming works
To begin with, a long metal strip - available in different widths - is unwound and guided through several sets of rollers arranged in a row, one behind the other. The roll forming process is carried out at room temperature, which is why it’s also known as 'cold rolling'. The big advantage: because the metal is processed at room temperature, all its original properties are retained or even improved.
Each pair of rollers further forms the metal strip until it reaches the desired cross-sectional shape at the end of the line, ready to be cut into the appropriate length. The more complex the profile shape, the more pairs of rollers required. The finished form is generally referred to as a rolled profile, roll-formed (custom) profile, custom profile, steel profile, metal section or simply as a steel tube.
In addition to open profiles, closed cross-sections can be produced with roll forming as well. With joining technologies such as laser welding and HF welding, the metal strip’s edges are brought together and welded shut. This is done as an integral part of roll forming, so that steel tubes with complex closed cross-sections can be produced cost-effectively.
Industries that utilize Roll Forming
While roll forming might not be the answer to every manufacturer’s needs, certain sectors have long benefited from making use of precisely fitted rolled profiles:
- Automobile and Vehicle Construction, e.g. cars, trucks, agricultural machinery, construction machinery, railway cars
- Energy Industries, e.g. solar energy, environmental technology, power grid infrastructure
- Construction, e.g. door and window construction, scaffolding, glass facades
- Furniture Building, e.g. adjustable table legs
- Agricultural Sector,e.g. animal husbandry, plant cultivation
- Domestic and Industrial Technologies, e.g. elevators, control cabinets, AC units
Opportunities & Advantages of Roll Forming
Here at Welser Profile, we’re both confident & enthusiastic about the high quality of our process. But what are the specific advantages of roll forming for your business? Let’s go through some of the biggest potential advantages:
- Implement Made-to-Measure Innovations
We live in fast-paced times: new developments happen at breakneck speed with one innovation following hot on the heels of the last. In the manufacture of roll-formed custom profiles, initial design drafts can be easily adapted to be suitable for roll-forming and then quickly implemented with tailor-made solutions under economically viable conditions.
- Manufacture Multiple Components
Roll forming is a fantastic way to cost-effectively add features along a longitudinal profile that wouldn’t be possible with extrusion, for example. Slits, holes, embossing or even pierce-clinch nuts can be added before or after the sheet metal strip runs through the rollers and is formed, with the advantage that the profile itself can fulfill several functions and still be processed with the utmost precision and high quality. Designers and product developers have the opportunity here to combine several components into one, establishing a more sustainable product development process.
- Optimize your Process Chain
The variety of process steps (stamping, bending, cutting, shaping, etc.) possible with roll forming allows for customization of the process chain, saving time and resources. It enables the direct delivery of the semi-finished part or the finished component straight from the system to the customer, where it can be immediately installed.
- Reduce Production Costs
Since several process steps can be linked in one production run and several functions can be integrated in the same profile at once, you can increase the economic efficiency of the entire manufacturing process. Final processes such as punching holes can be done simultaneously without the extra cost of temporary storage or transportation. Additionally, a single multifunctional custom profile can replace a combination of several assemblies. In times of raw material scarcity, sustainable supply chains and scrap recycling also represent a cost factor that carries weight with a responsible supplier.
- Get the most out of Steel, Stainless Steel & High Strength Non-Ferrous Metals
Since the metals are processed at room temperature, their integral properties are largely retained. In this way you can take advantage of all the characteristic qualities of the material, such as the high strength and ductility of steel, while at the same time processing it with great precision. It’s always more cost-efficient to produce a custom-fit custom profile instead of processing a standard profile and then adding several downstream steps.
- Economize with Customization on a large Scale
Roll forming is almost an infinite process, capable of producing millions of meters of accurate, tightly toleranced custom profiles. The more that can be produced in one run, the better - the higher the quantity, the more profitable it becomes.
- Unlimited Production Quantity with consistent Quality
Unlimited repeatability and exceptional quality management are two of the most important qualities of roll-formed steel profiles. This leads to consistently, precisely processed roll profiles, regardless of the number of pieces and allows for the problem-free reproducibility of new editions.
Limitations of Roll Forming
Since every requirement is unique and requires different solutions, it’s important to be clear about the limits and disadvantages of the roll forming production process to help you make sure it fits your needs:
- Small Production Quantities are rarely worthwhile
A prerequisite for high-quality roll forming are the high-quality and sometimes design-specific tools that can be individually manufactured for each customer. Since these tools are then custom-made and manufactured under strict secrecy, it offers a real competitive advantage, but it’s also a significant cost factor that needs to be considered. The roll profiling process is therefore usually only economically attractive when looking at minimum quantities of 3,000 - 5,000 meters. - Prototypes need to be manufactured In-House or with an External Partner
Although we at Welser Profile can, in principle, produce prototypes of approx. 10 running meters, you’d need to be fairly sure of subsequent production in large quantities to make it worth the cost. In most cases it makes more sense to produce model designs yourself or with an external partner (e.g. a local craftsman). To illustrate functionalities and shapes, we use plastic prototypes from the 3D printer. - Roll Forming is (Mostly) only suitable for Steel and Non-Ferrous Metal Components
The roll forming process can be used to produce high-strength profile cross-sections from steel, stainless steel and non-ferrous metals. It is less suitable for aluminum, for example. Since, as always, the exception proves the rule, certain aluminum alloys are definitely suitable for cold rolling. - Everything has its Limits
With roll forming, profiles can be produced with a thickness of 0.3 to 8.2 millimeters, with a strip width of up to 1,000 millimeters, with a profile length of up to 27,000 millimeters - logistical rather than production-related restrictions are decisive here - and with a profile height of up to 320 millimeters.
Roll Forming as an Alternative to Extrusion
In almost every product development process for custom profiles, the question arises at some point: steel or aluminium? Of course, it's not just about the material properties, but also about the process itself. Roll forming (steel, stainless steel, non-ferrous metals) should be used instead of extrusion (aluminum):
- if the required metal can’t be extruded.
- if it’s not economical to insert extra functions along the longitudinal section in an extruded profile t.
- if an extruded profile cannot be produced precisely enough, i.e. better tolerances can be achieved with roll profiling
What makes a good Roll Former & Profile Vendor
There may be certain reasons that would call for avoiding the use of custom profiles - and in most cases, the reasons lie not with the process itself, but with inexperienced providers who implement projects inefficiently. Here’s what to look for in a good manufacturer and dealer of rolled profiles:
- Clear Separation between Custom Profiles and Off-The-Shelf Products
If you need a standard profile that requires little or no editing, then choose a supplier with a selected range. If your profile needs to fulfill very individual and even multiple functions, then contact a roll profiler who specializes in custom profiles.
- Diverse Range of Solutions
A wide range of solutions and Use Cases from a wide variety of industries shows the creative problem-solving skills and flexibility of an experienced manufacturer of roll-formed custom profiles.
- Design Support
A good profile manufacturer won’t leave you unaccompanied with your design: they should provide you with advice and support right from the early stages of product development. Since the possibilities of roll forming are so diverse, it’s impossible to know them all without the help of a pro.
- Producing their own Tools
Ideally your profile vendor should produce all the rolling and punching tools themselves and customize them for each customer with confidence.
- Short Delivery Times & good Storage Options
You’ve got to think beyond the factory doors: you need a reliable partner who’ll work with you when it comes to delivery times, logistics, assembly options and much more.
- ISO-Certificate
A reliable supplier of roll-formed custom profiles in large quantities should be able to guarantee a high standard of quality across the entire supply chain. These include ISO certificates such as ISO 9001, ISO 45001, ISO 14001 and ISO 50001.
Conclusion: Roll Forming can do more than you might think
Roll forming, roll profiling, cold rolling - call it what you will - produces tailor-made custom profiles out of steel, stainless steel and other non-ferrous metals. So far, so good. In the bigger picture, it brings innovations to life: concepts you might have only conceived of yesterday can be ready to implement tomorrow. These profiles, with their wide range of functions and precise tolerances are ideally suited to facilitate the most sweeping product developments.
Read more
Similar articles
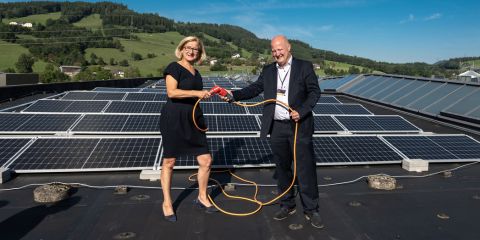
Photovoltaics: Green Steel for Green Energy
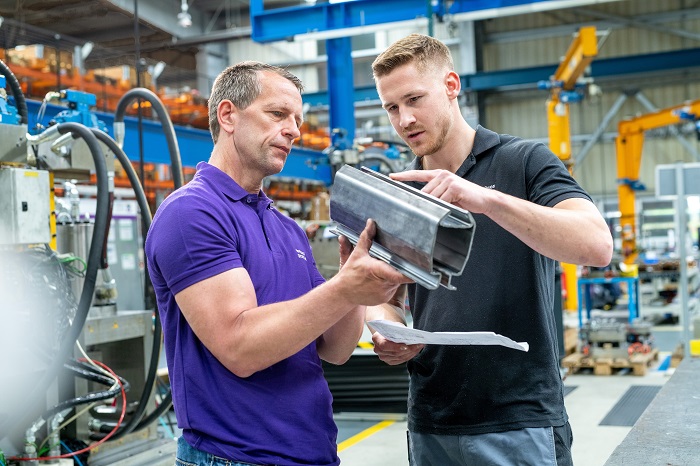
10 unbeatable Features of roll-formed Steel Components
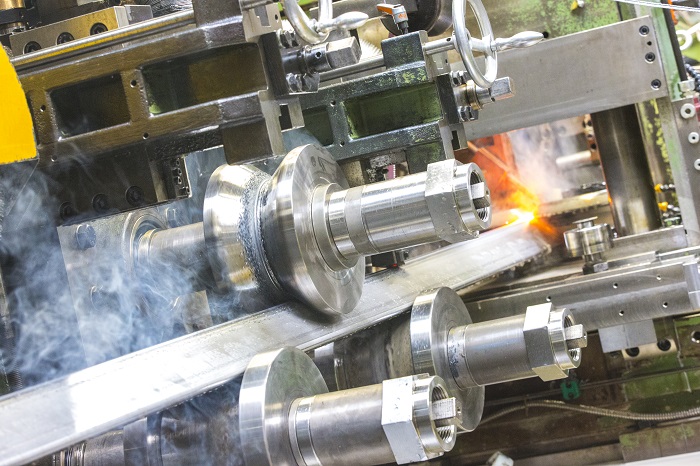