Is Steel the new Aluminum? Comparing 2 strong Materials
Reaching climate targets in the upcoming years is an increasingly important consideration in industry: in many companies, sustainable product development is expected to help reach these goals. Accordingly, decision makers across the board are asking the question: which material will be best suited for product development and manufacture in the long run? Be it in mechanical engineering, construction, or the food industry – the search for sustainable materials and innovation is in full swing.
More than likely, this will include the comparison of aluminum and steel. The advantages and disadvantages of the two materials are no longer viewed as superficially as they were in the past. Both materials and processing methods are constantly evolving and it is worth examining the alternatives in order to find the best solution for the desired component.
Aluminum or steel – which is the best choice for your component? Read on to learn more about the future potential of these two materials.
3 Advantages of Components made of Aluminum (Aluminum Profiles)
Hardly any industry can do without aluminum these days. The material, which has been rapidly industrialized since the 19th century, was used early on for the construction of light metal ships and has rapidly become a popular material in the automotive, aerospace, electrical, furniture, food and packaging industries.
This is due to the variety of advantages of components made of aluminum, exemplified here by aluminum profiles:
- Easy to produce:
In many cases, complex cross-sections made of aluminum involving multiple chambers and different wall thicknesses can be produced more cheaply than steel profiles, since aluminum is well suited for extrusion due to its high malleability. - Low-cost production for smaller quantities:
Extrusion as a production process also allows for a more cost-effective manufacture when dealing with smaller quantities of aluminum profiles. - Lightweight material:
Compared to steel, the lightness of the base material of aluminum is one of its major advantages. Its density is 2.5 g/cm3 – which is just under a third of that of steel at 7.8 g/cm3. Aluminum also forms a natural anti-corrosion layer on its own.
Because of its lightness and cost efficiency in the production of smaller volumes, profiles made of aluminum are popular for window frames, rail cars, car bodies and aircraft. Thanks to diverse and technically sophisticated processes aluminum parts can also be welded and brazed.
4 Advantages of Profiles made of Steel
Steel is a very resistant material that was discovered more than 5,000 years ago. Statistics show that steel has been the most important raw material in terms of volume for many decades and is mainly used in the automotive industry, construction, mechanical engineering, metal processing and other sectors.
The most important advantages of steel include the following:
- High strength:
In order to produce particularly strong profiles, such as very narrow frames for large glass fronts, significantly less volume is required when using steel than with aluminum, for example. This is because rigidity is achieved much more quickly thanks to the high strength of steel. - Significantly higher melting point:
The melting point of steel is over 1,500°C, while the melting point of aluminum is 660°C. This results in the superior high-temperature strength of steel. For this reason, fire protection doors and security doors, for example, are always made of high tensile steel. - Wide variety of materials:
There are more than 2,500 standardized types of steel worldwide, meeting the right requirement for nearly every component: be it high-quality stainless steel for the food industry, high strength steel for window construction or acid-resistant steel for chemical laboratories, there’s a type of steel the fits the job.
Generalized statements about cost efficiency can be difficult to make when comparing aluminum and steel. However, steel more often than not proves to be more cost effective in larger quantities.
Roll Forming (Steel) vs Extrusion (Aluminum)
Overall, the production of roll-formed components made of steel and extruded components made of aluminum is similarly economical. Depending on the design and quantity, the cost-benefit barometer tips in favor of one material or the other. The differences between the two processes become interesting in the light of the following aspects:
- Integrating holes:
During roll forming, holes or other functionalities can be integrated directly into the steel profile on the production line using additional tools - without the need for an additional processing step. - Tolerances:
Unlike extrusion, roll forming enables production with very tight wall thickness tolerances. - Lower tool costs:
Extrusion presses score with low tool costs, which is an advantage especially for small batch sizes. - Finishing:
Unlike extrusion, roll forming allows for low-cost finishing. If required, very high-quality surfaces can also be produced, for example, without visible roller marks.
How to switch from Aluminum to Steel successfully
One pioneer in the automotive industry has already demonstrated that the switch from aluminum to steel can be both successful and worthwhile: Since the mid-2020s, we’ve been supplying large quantities of roll-formed tunnel connectors made of steel to the BMW Group, replacing a component previously made of aluminum. After joint testing, this has proved to be lighter, and due to large order volumes, less expensive.
Here are 3 tips to keep in mind when considering a change from aluminum to steel:
Tip N° 1: Ask yourself how high the vertical Integration of your Component should be.
Is it, for example, advantageous to integrate holes in your component? If so, then it’s worthwhile to look into the advantages of roll forming, since the perforation takes place in the same manufacturing process. This is different with aluminum extrusion, where holes can only be punched afterwards, requiring an additional step in the production process.
Tip N° 2: Keep looking for Perfection.
Some people say, if it ain’t broke, don’t fix it. But we say there’s always room to improve and get closer to perfection! Is it advantageous if your component is more space-saving, more solid or more elastic ? Then dare to ask the question if steel, aluminum or even a completely different material is the better choice than what you are currently working with.
Tip N° 3: Develop your new Component together with Experts.
Like the automotive industry, other branches look back on many years and decades of proven stamping techniques and numerous integrated aluminum parts, and rightly so. To open up to a new technology such as roll profiling you need a profitable basis of knowledge, experience, and lessons learned from past mistakes. In joint developments with experienced specialists, the suitable materials, ideal shapes and best machines can be determined, and the feasibility of the newly designed component can be checked.
Conclusion: Steel vs. Aluminum requires careful Consideration
Hopefully it’s evident after reading this post that deciding whether aluminum or steel is right for your component requires some careful consideration on multiple fronts. Roll profiling with steel goes hand in hand with a new level of flexibility and can enable you to take advantage of some fabulous new functions. In view of the ambitious climate targets many European and global companies are setting, steel is rightly moving into the spotlight thanks to its thanks to its promising potential to reduce the CO2 footprint with alternative production processes.
Not found what you are looking for yet? Let's find the best material for your projects together.
Read more
Similar articles
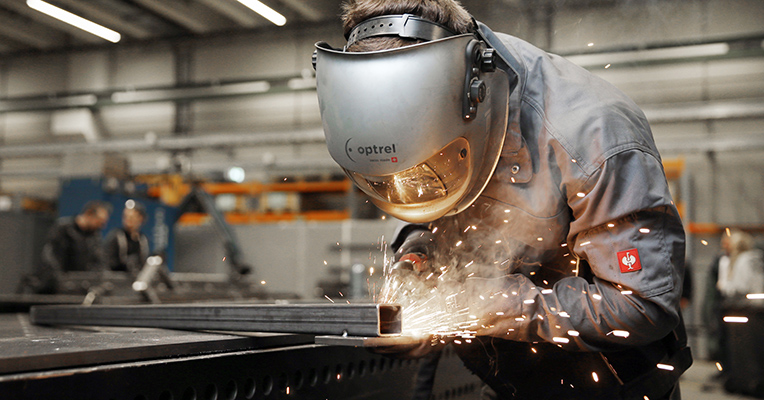
What’s really possible with Welded Custom Profiles?
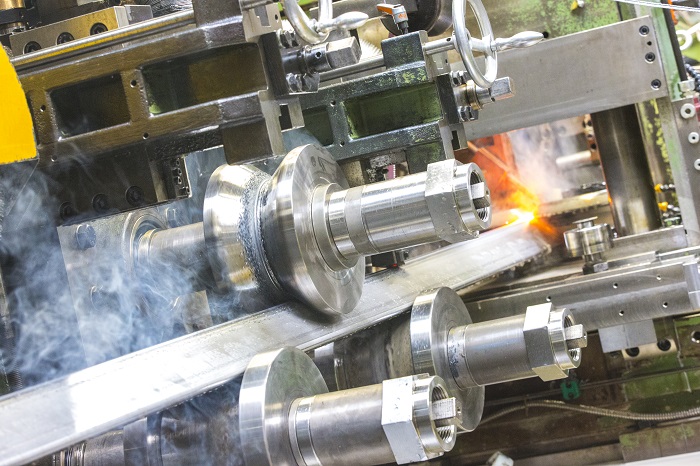
Is Steel the right Choice for you? Here's what Designers & Product Developers need to know
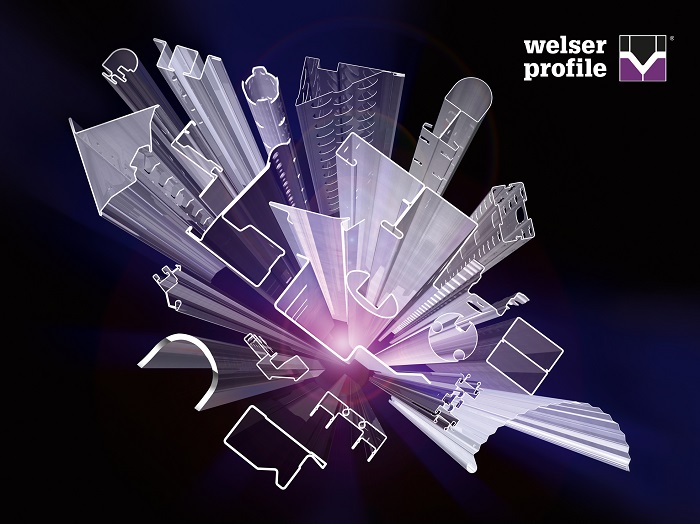