10 unbeatable Features of roll-formed Steel Components
In every industry, there are as many required components as there are different materials and manufacturing processes. Steel alone comes in more than 2,500 types and grades, and each can be processed in very different ways. Roll forming (also known as roll profiling or cold rolling) is a production process that offers flexible solutions and products that meet the relevant standard requirements and bear the mandatory CE mark (i.e. all EU-wide requirements for safety, health and environmental protection have been met). Various steels are processed and formed into extremely precise and high-quality cross-sections.
To give you an overview of some of the advantages of roll-formed steel components, we’ve summarized 10 features of roll formed steel that can’t be beat:
1. Repeatability
When processing using roll forming, a sheet of steel, stainless steel or non-ferrous metal is guided through several pairs of rollers and formed into a specific shape. Since these rollers are designed and manufactured individually for each component, significant cost savings can be achieved, especially with longer production runs, because the production process can be repeated as often as required. This repeatability also ensures a high-quality guarantee over many years, since one set of correct measurements can be used to meet long-term production requirements.
Repeatability becomes an unbeatable quality feature if the client's customer-specific processing requirements are taken into account right from the start, because roll forming allows for much more precise manufacturing tolerances. For example, dimensional accuracy can be maintained already 50 millimeters from the beginning of the bar of a head jump – a significantly smaller gap than the industry standard of 250 millimeters from the beginning of the bar.
2. Longevity
Steel is renowned for hardness, robustness, stability, durability and 100% recyclability. These advantageous material properties are used extensively in many industries and are essential for many components. For example, bridge structures, buildings and national landmarks such as the Eiffel Tower must withstand earthquakes, winds, fire, traffic loads and other extreme environmental stresses over a long period of time. The durability of steel as a raw material is clearly an unbeatable quality feature in the construction industry as well as in product developments in mechanical engineering or in the automotive industry.
From stainless steel to hot-dip galvanized steel or high-alloy and high-strength steel types, all steels have one thing in common: durability and strength. Durable components made of steel also score points for:
- the large number of different steel grades and types of steel for individual requirements
- numerous alloys that allow for even longer product life cycles
Read here why the BMW Group prefers roll-formed steel connecting beams over aluminium.
3. Reproducibility
Because roll forming is a repeatable yet precise process, it enables a wide variety of components to be manufactured. For example, long profiles for rail car construction can be produced with a wide variety of functionalities, which can be precisely connected again and again in each new edition. Reproducible roll profiles made of steel in high quality and quantities are possible, since the system and tools for roll profiling are highly customized. In this context, an increase in quantities and cost-effectiveness is also possible: roll forming is often more economical than conventional methods such as edging or other sheet metal processing shapes, especially when it comes to larger quantities.
4. Precision
With roll forming, the desired cross-sections can be very precisely produced, from semi-finished parts to finished products. Thanks to intensive preliminary planning and precise feasibility studies, the risks have been almost completely eliminated and the success of the product development is guaranteed. Numerous individual processes such as punching, embossing, notching, and subsequent finishing processes such as laser cutting and/or surface finishing are carried out in a modular manner. These work steps are evaluated in an integrative manner with a view to the entire development cycle.
Caption: With the Welser Creator you can create simple or complex cross-sections precisely and easily.
5. Reduction of Components and Process Steps
Sometimes, less is more. Instead of connecting several assemblies with each other, various functions and shoring requirements can be integrated into one roll profile during roll forming. Historically, steel was often bought as unprocessed bar stock and only then sawn, punched, lasered, filed, etc. Roll forming replaces this classic manual work - several process steps are paired, since a thin sheet metal strip is formed from the start in such a way that it fits the individual requirements. This saves time, resources and waste. After all, precise and sustainable planning also leads to avoiding raw material waste and reducing components – which is, by the way, one of 7 Innovations in Mechanical Engineering.
6. Malleability
Due to the stability of steel, forming with conventional processing methods such as edging has limited applicability, as the tools used need to hit and bend the material from a specific direction. This is different with roll forming, where the use of multiple rollers ensures diverse formability. The profiling system ensures that the metal sheet has a sufficient contact surface so that the tools work optimally and multiple formations can be successfully executed.
7. Strength & Flexibility
Steel is strong enough to carry heavy loads, and flexible enough not to break. The modulus of elasticity (E modulus for short) or elongation modulus is a material parameter from materials engineering and describes the proportionality between tension and elongation of a solid material, i.e. how much a material yields when a force is applied. The modulus of elasticity of steel is 210,000 N/mm² and is therefore very robust, but also tough and elastic. A quality feature that is essential for heavy loads with trucks or cranes.
8. Heat Resistance
The E Modulus and the melting point are proportional to each other - the high melting point of 1,400° Celsius makes steel fireproof against induced heat and flames. This is why steel is the primary metal used in fire protection (e.g., fire doors). In comparison: Aluminum melts at 660° Celsius and is therefore far less heat resistant. A high melting point is essential in industry and building development. Affected constructions must be built in such a way that, for example, no flames from a spontaneous fire can shoot through the door, and the door must not warp. There are rigid and high standards for fire resistance class construction. The heat resistance of steel is therefore an essential quality feature, especially when it comes to fire protection.
9. Multiple Functionalities
In the manufacture of roll-formed steel components, the material properties are combined with the advantages of the component geometry and the production process. This is a unique advantage: some cross sections can only be produced by roll profiling. For example, a hole can be punched at a point during the manufacturing process that another tool would not be able to reach in the finished component state. Other functionalities include the introduction of fastening and thread solutions for a ready-made built-in part.
10. Diverse Material Classes
The numerous different grades and material classes of steel offer a suitable solution for every component. Hot-rolled structural steel, for example, has 30 to 40 different materials with different yield points, elongations at break and surface characteristics. Depending on requirements, the various steels can be ductile and tensile or more rigid and robust, heavily textured or smooth, and much more. Depending on the intended use of the roll profile, a material class can be selected that suits the individual requirements of the component. This diversity is a quality feature of steel that few other materials can match.
Conclusion: Precise. Resource-Saving. Consistent.
Roll-formed steel components have unbeatable quality characteristics and represent an economically attractive alternative: bespoke, repeatable and high quality. Due to its precision and flexibility, the processing method saves resources and time, while finished surface-treated parts can be installed directly. In order to best take advantage of the quality features of roll forms, the experts at Welser Profile are in close contact with our customers to develop individual profiles to suit their needs. We have been producing customer-oriented solutions for over 60 years and are happy to support you with your individual requirements and desires.
Would you like to learn more about the life cycle assessment of steel? Download our latest whitepaper now free of charge.
Read more
Similar articles
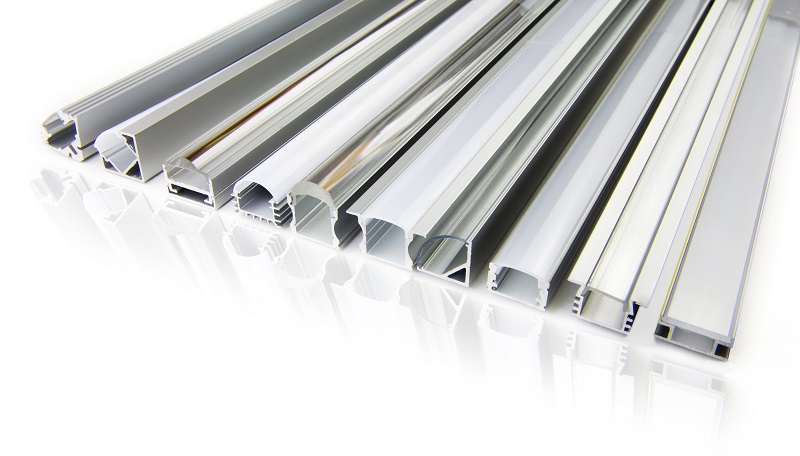
Is Steel the new Aluminum? Comparing 2 strong Materials
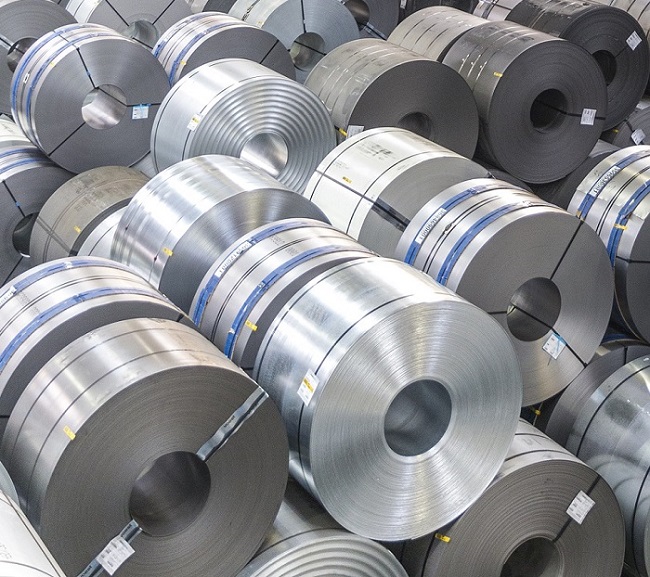
Is a Roll Former a better Alternative to the Classic Steel Distributor?
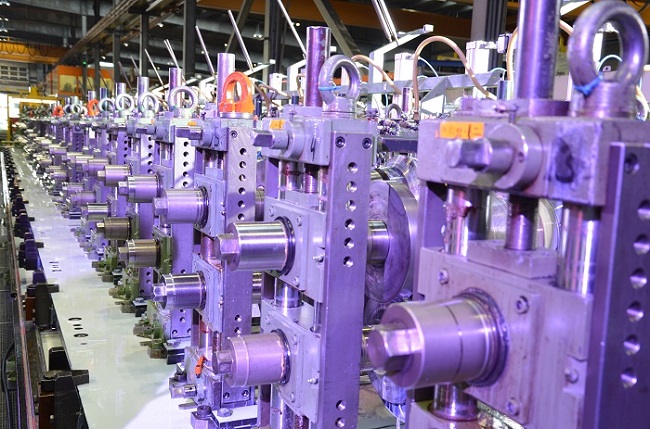