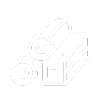
Green Steel For a Climate Neutral Future
- Chapter I Introduction
- Chapter II What is Green Steel?
- Chapter III Strategies for decarbonizing the steel industry
- Chapter IV How sustainable is steel?
- Chapter V Advantages & disadvantages of steel
- Chapter VI Steel vs. Aluminum
- Chapter VII Roll forming with green steel
- Chapter VIII Quality features of roll forming with steel
- Chapter IX Steel for mechanical engineering
- Chapter X Availability of green steel
- Chapter XI Local Sourcing
- Chapter XII 5 tips for dealing with raw material shortages
- Chapter XIII Sustainability at Welser Profile
- Chapter XIV Conclusion: A climate-neutral future is only possible together
Introduction
- no more net greenhouse gases are emitted by 2050,
- economic growth is decoupled from resource use and
- no people nor region have been left in the lurch.
This goal also presents steel producers and processors with major challenges. Although the finished end product, steel, is an extremely sustainable material, its production has anything but a positive impact on the climate balance. With the currently predominant production process using the blast furnace route, the steel industry is by far the largest direct CO₂ emitter.
Accordingly, leading manufacturers want to put steel production on a climate-friendly footing using innovative processes and fully convert their production to Green Steel by 2050. In this article we will summarize how this can work and why steel, in combination with modern processing methods such as roll forming, is the right step towards a climate-neutral future.
Green Steel - What exactly is it?
The term “Green Steel” is used to describe steels with improved CO₂e balance. It refers to both CO₂e-neutral steel and CO₂e-reduced steel, although the production of completely CO₂e-neutral green steel is not yet possible today.
Leading manufacturers such as voestalpine and thyssenkrupp have set themselves the goal of completely CO₂e-neutral steel production by 2050 at the latest. The idea is to achieve this by converting manufacturing processes from classic blast furnaces with high CO₂e emissions to processes with a better greenhouse gas balance. The production of CO₂e-reduced steel is already achievable through the use of hybrid technologies, although it often involves a lot of effort and costly retrofitting of the steelworks.
More Information
Strategies for Decarbonizing the Steel Industry
So far it’s been possible to develop some promising strategies for decarbonizing the steel industry. Their advantages lie primarily in the significant reduction of CO₂e emissions and the creation of more sustainable steel production. The disadvantages include, among other things, the development of the necessary infrastructure and covering energy requirements from renewable sources.
Using Green Hydrogen
The use of green hydrogen as a reducing agent is an extremely promising method for decarbonizing steel production. It’s obtained from renewable energy sources through electrolysis and is a clean alternative to coal or coking coal, as its combustion only produces water vapor instead of CO₂e. When using green hydrogen, existing blast furnaces or direct reduction technologies can be retained. Steel producers do not, therefore, have to convert their factories for the new process.
But it still doesn’t work without large scale new investments. An extensive infrastructure is required for the production, storage and distribution of hydrogen. And the high energy requirement for the electrolysis needed to produce it also requires a massive expansion of renewable energy sources.
Electrification of Steel Production
With this method, steel production is switched from the previous blast furnace route to electric arc furnaces (EAF). Instead of coal, the heat required for the smelting process is generated using electricity. This means that CO₂e emissions can be significantly reduced if the electricity used comes from renewable energy sources. This production process offers a high degree of flexibility in the production of different types of steel and in the recycling of used steel.
In order to cover the increased electricity requirements when switching from blast furnaces to electric arc furnaces, an expansion of renewable energy sources is also essential. Additional effort is also needed from the steelworks themselves, which in most cases have to convert their existing infrastructure to use electric arc furnaces.
Carbon Capture and Storage (CCS)
With this approach, the CO₂e emissions released during steel production are not released into the atmosphere, but are stored in underground facilities. This means that CO₂e emissions can be significantly reduced even if we stick to the current blast furnace route. This method is also suitable for combination with the hydrogen or electrification process.
However, a comprehensive and economically sensible use of the CCS method is currently not quite in sight. The capture of carbon dioxide as well as its transport and storage require significant investments and the development of suitable infrastructure.
How Sustainable is Steel?
In addition to the manufacturing process, steel is characterized by its material properties and a high degree of sustainability. While the prevailing manufacturing process still releases enormous CO₂e emissions via the integrated blast furnace route, amounting to around 1.7 tons of CO₂e per ton of crude steel, the finished end product is actually extremely climate-friendly and resource-saving. This is due in particular to the following 3 aspects:
- High proportion of scrap recycling:
Due to its longevity and corresponding recycling processes, 84 percent of the steel produced worldwide is still in use, according to a current statistical report by the Steel Association. Accordingly, 35.7 million tons of crude steel were produced in Germany in 2020 and 15.8 tons of steel scrap were used. - Process-related efficient use of materials:
Processes such as roll forming produce relatively little waste. And even the small amount of steel scrap produced during processing can be reused in the steelworks or forges. - Steel is recyclable:
Almost all of steel can be recycled without any loss of quality. According to a statistical report by the Steel Association, recycling saves more than 1.5 tons of iron ore and more than 0.65 tons of coal per ton of steel produced.
Advantages and Disadvantages of steel
Due to its material properties, steel has been indispensable across many industries for decades and, according to statistics, is the most important material in terms of quantity. However, steel also has its disadvantages and is not always the best choice. Here is an overview of the most important advantages and disadvantages of steel for designers and product managers.
Advantages:
- Static load capacity & elasticity
Steel is characterized by a high static load-bearing capacity that is maintained over a very long time. Due to its high modulus of elasticity, steel also remains stable over large areas. - Longevity
Steel structures are extremely durable and usually last for several decades. If the material is provided with corrosion protection, its durability can be further extended. - Dynamic Stress
Due to its material properties, steel is particularly suitable for use where parts are alternately subjected to particularly strong pressure and then hardly any, e.g. for the construction of hydraulic pumps. - Variety of alloys
Using a wide variety of alloys, steel can be optimized for many different requirements and applications. - Recyclability
Steel is recyclable to a very high degree and steel scrap can be used, for example, in the electric arc process to produce new steel. - Coefficient of thermal expansion
Due to its relatively low coefficient of thermal expansion, steel is ideal for buildings that are exposed to high levels of heat due to solar radiation. - High fire resistance
Steel and steel composite parts are classified as non-combustible building materials, and accordingly play an important role in fire protection, e.g. in the production of fire doors. - Variety of steel types
There are now more than 2,500 types of steel available on the market that optimally cover almost every individual requirement. From structural steels, to alloyed and unalloyed steels, to tool steels and steels of various degrees of hardness. - High availability
Even though the availability of many raw materials has become more scarce recently, there are no serious delivery problems with steel, especially in Central Europe. Conventional steels in particular are still easily available here.
More Information
Disadvantages:
- Weight
Steel has a significantly higher weight than aluminum, for example, and therefore has a weight disadvantage as a building material. However, due to the high strength of the material, this disadvantage can usually be compensated for by utilizing a thin design. - Corrosion protection
In many environments, unalloyed steel is significantly more susceptible to corrosion than, for example, aluminum, which is why an additional coating is often required to make constructions more resistant. - Processing
Due to the heating during forging or welding and the subsequent cooling, the molecular structure of the steel changes and stresses arise in the material. This problem can be avoided, for example, using a process such as roll forming, where the manufacturing material is formed at room temperature. - Cost assumption
This is not a material-related disadvantage in the narrower sense. However, if steel (which may in fact be the most suitable material) is excluded at an early stage for supposed cost reasons, this has a negative impact on the product quality of the respective component.
Steel or Aluminum - Which Material is Better?
In the long term, which material is best suited to reconcile operational innovation and social sustainability requirements - be it in mechanical engineering, construction or the food industry? We’ve already heard convincing arguments for components made of steel in the previous chapter, so let’s now look at the most important advantages of aluminum profiles:
- Easy production
Due to the significantly softer material and the associated formability, complex continuous cast sections can be produced with comparatively little effort. - Cost-effective production
Optimized production routines for aluminum profiles allow the cost-effective production of profiles in smaller quantities. - Lightweight material
With a significantly lower density than steel, aluminum wins out in direct comparison for lightness. - Uncomplicated processing
With the help of modern machining processes, aluminum parts can now be easily welded and soldered.
Both steel and aluminum are high-quality materials with many advantages. Generalizations that clearly show one material or the other having an advantage can’t really be made in just a direct comparison. Rather, each project depends on the individual requirements. However, steel always proves to be more cost-effective when ordering and producing larger quantities. And roll forming with steel in particular enables completely new perspectives in terms of flexibility and functions that were never possible before. Last but not least, the climate footprint will play a greater role in the choice of materials in the future and steel, especially green steel, will continue to come into focus.
More Information
Roll Forming with Green Steel
The term “Green Steel” refers to steel with an improved carbon footprint achieved through climate-friendly manufacturing processes. The new manufacturing processes do not change the quality or material properties of the steel itself. Green steel is just as suitable for roll forming as steel that was traditionally produced via the blast furnace route.
When it comes to sustainability, roll forming checks off three important boxes:
- Fewer Process Steps:
Roll forming combines several routines in a single production step that, in other processes, are carried out individually and downstream. These include, for example, sawing or punching. - More Efficient Use of Energy
During roll forming, the required profiles are manufactured at normal room temperature. In contrast to other processes, there is no need to make the steel more flexible using enormous amounts of energy and high temperatures. - Maximized Usage of Materials
Roll forming produces comparatively little material waste. Most of the starting material flows into the desired end product and the remaining steel scrap can be melted into new steel in the electric arc furnace as part of secondary steel production.
Quality Features When Roll Forming with Steel
The possible applications of roll formed steel components are almost unlimited and offer unparalleled development potential for flexible products and solutions. Let’s look at some outstanding quality features that make roll-formed steel components so important for the industry.
- Repeatability
The rollers required for roll forming are individually designed and manufactured for each component. Once the rollers have been manufactured, the production process can be repeated as often as desired with consistent material quality. - Longevity
Steel is robust, stable and durable. With these material properties, steel is the go-to wherever structures and components have to withstand high loads over a long period of time. - Precision
From semi-finished products to finished parts, cross-sections are produced with high precision during roll forming thanks to intensive preliminary planning and exact feasibility tests. - Reduction of components and process steps
During roll forming, a thin steel strip is integrally shaped so that it meets the individual requirements. Subsequent processing procedures are no longer necessary. This saves time, resources and waste. - Formability
During roll forming, the profiling system and tools enable multiple reshapings of the production material. - High flexibility combined with necessary strength
Steel is extremely hard and at the same time relatively flexible. Its modulus of elasticity, i.e. the material parameter for the proportionality between tension and elongation of a solid material, is three times as high as that of aluminum. - Heat resistance
With a melting temperature of 1500° Celsius, steel is extremely resistant to induced heat and flames. Particularly when it comes to fire protection, the heat resistance of steel becomes a key quality feature. - Multiple Functionalities
The specific manufacturing techniques in roll forming allow almost limitless functionalities, as the properties of the material are combined with the advantages of the component geometry and the production process. - Diverse material classes
The diverse grades and material classes of steel offer a suitable solution for every component. Just select the material class that best suits the individual requirements of the component for the respective roll profile.
Steel for Mechanical Engineering
A product development process that is as climate-friendly as possible is also becoming increasingly important for designers in mechanical engineering. At the same time, the material must meet high requirements in terms of durability, quality and innovative strength. Since the widespread availability of green steel is not possible in the foreseeable future, the following materials are recommended for high-quality mechanical engineering:
- Ultra high strength steels
Ultra-high-strength steels are alloy steels with a higher minimum tensile strength. They are wear-resistant and are characterized by high heat resistance. Ultra-high-strength steels are used wherever relatively low weight and high strength are required, for example in lightweight construction, aerospace and vehicle construction. - New structural steel
While designers looking for a precisely fitting material would probably not be happy with conventional structural steel, special alloys or particularly corrosion-resistant coatings open up new possibilities for the building and construction sector as well as in industrial technology. - Stainless steel
Regardless of whether it is austenitic, ferritic or cold hardened - stainless steel is and remains closely linked to mechanical engineering and is particularly indispensable in industries with strict purity requirements due to the lack of adequate alternatives. In addition to the food industry, stainless steel is also used in packaging and filling systems, but also in tunnel and rail vehicle construction. - Special alloyed metals
Both in mechanical engineering and in many other industries, special alloyed non-ferrous metals such as nickel or titanium are often the only real - albeit very expensive - alternative to “real” steel. They are characterized by their particular resistance to chemical substances and are therefore primarily used in special systems in the chemical industry, e.g. in the production of hydrochloric acid.
Weiterführende Infos
Availability of Green Steel
Although the technologies required for production already exist, there is still a lack of widespread supply of green steel. The reasons for this are diverse:
- Supply chains are lagging behind
Today's supply chains are not yet effectively designed to reduce CO₂e in the product, as neither green hydrogen nor other necessary components (DRI or HBI) are currently available on the market in sufficient quantities. - Uncertainty in supply
CO₂e-reduced steel is currently only offered by very few manufacturers. Therefore, to reduce risky dependencies, most companies choose to purchase conventional steel. In the future, this lack of demand will turn into a bottleneck issue if not enough CO₂e-reduced steel can be supplied compared to the potential demand.
- Dependence on grey steel
There are numerous product areas in which the use of CO₂e-reduced steel is currently unthinkable due to comparatively high purchasing prices. Especially if the end users are not prepared to spend more money on the use of green steel. - Risk in redirection of usual supply chains
According to current knowledge, the performance and product quality of green steels corresponds to that of conventional gray steels. However, as long as there is no reliable evidence of this due to a lack of available processes and corresponding practical tests, the redirection of usual supply chains in the direction of CO₂e-reduced steel remains associated with a residual risk.
Local Sourcing - Regional Procurement Pays Off
Regional sources of supply pay off in steel processing, for customers and the climate alike. The geographical proximity to the respective suppliers ensures the flexibility and availability of materials and services. The short transport routes ensure the lowest possible levels CO₂e pollution.
At Welser Profile, we have always placed great value on regional procurement, both for roll forming materials and for auxiliary and operating materials. Wherever possible and sensible, we buy from suppliers close to our production sites.
Long-term cooperation with our European suppliers guarantees us an excellent regional supply of materials. But of course we are also dependent on many outside factors in the direct environment of our most important partners. The omnipresent shortage of raw materials caused by the pandemic has not left Welser Profile untouched.
5 Tips for Dealing with Raw Material Shortage
The lack of suitable raw materials affects the manufacturing processes of industrial companies and sometimes leads to economically painful production losses. And even if a raw material is usually relatively readily available, there are a number of different factors that repeatedly lead to shortages:
- High demand for certain types of steel
- Increase in customs duties or enforcement of new punitive tariffs
- Failure of important suppliers
- Force majeure
- Competitors suddenly become active
Although the sufficient availability of materials can never be guaranteed 100%, the following 5 practical tips for dealing with raw material shortages can still significantly improve the initial situation:
- Rely on raw materials that will be available in the future
Instead of just looking at the cheapest option for producing components today, the future availability of raw materials must also be taken into account. Roll formed components made of steel, for example, are based on a raw material that will continue to be available in many variations in the future. - Buy raw materials locally
Local sources of supply pay off. In addition to building good relationships with the regional steel industry, this results in faster and shorter delivery routes, even if raw materials are becoming scarce globally. - Estimate your needs holistically
Your own raw material requirements should always be determined holistically on the basis of a wide variety of consideration levels. A transparent exchange with suppliers and partners is essential. The more perspectives you take into account regarding potential shortages, the better supply will be guaranteed. - Think proces- integrated
Material availability can be determined through process-integrated solutions, e.g. in roll forming. Because when calculating larger production quantities, even small material savings for a component have a major impact on the quantity required. - Maintain relationships
Good mutual relationships with partners and suppliers always pay off and help to overcome times of crisis. In addition, they are an important basis for establishing a strong local industry. At Welser Profile, for example, we are working with leading manufacturers to drive forward the transformation to CO₂e-neutral steel production in Europe.
More Information
Sustainability at Welser Profile
Environmental awareness is built into our DNA at Welser Profile, and it’s part of all areas of our operational value chain. We are committed to sustainable production and source our manufacturing materials from local suppliers. At the same time, we pursue a holistic approach to reducing our CO₂e footprint. We prefer to distribute steel via rail transport, process it in a resource-saving manner using roll forming and recycle the little scrap that is generated for reuse in the steelworks.
We also let customers and project partners share our know-how on sustainable steel and offer comprehensive support in the climate-friendly implementation of their projects. We are also expressly committed to the United Nations' sustainability goals, which we pursue, among other things, through the following measures:
- Objective: CO₂e neutrality in terms of energy sources by 2026 (through our own PV systems, our own wind power plant and the purchase of green energy)
- Provision of e-charging stations
- 100% green external electricity in Austria and Germany
- Continuous conversion of lighting fixtures to LED technology
- “Efficient Production Plant” project and various other energy efficiency projects
- Reusable packaging for spare parts
- Roll recycling – reworking roll tools that are no longer used
- Transport of primary material or scrap removal by rail
- Predominant use of forklift guidance systems, electric forklifts
- Procurement of raw materials on the European market
- Survey of Corporate Carbon Footprint (Scope 1-3)
- Maintaining the certified environmental management system according to ISO 14001 and energy management system according to ISO 50001
More Information
A Climate-Neutral Future Can Only be Achieved Together
Green steel paves the way to a climate-neutral future for several industries by combining the material-related advantages of steel with sustainable production. Now it’s up to all of us to consistently follow this path. To the manufacturers, the product developers, the processors, the legislator and of course the end consumer. Ultimately, the demand for green steel also means, in the short term, a departure from usual routines and a step out of the comfort zone. But this much is certain: only if we always choose the most sustainable option today from among all the available alternatives will we ensure a climate-neutral future for future generations.
Current Blog Articles
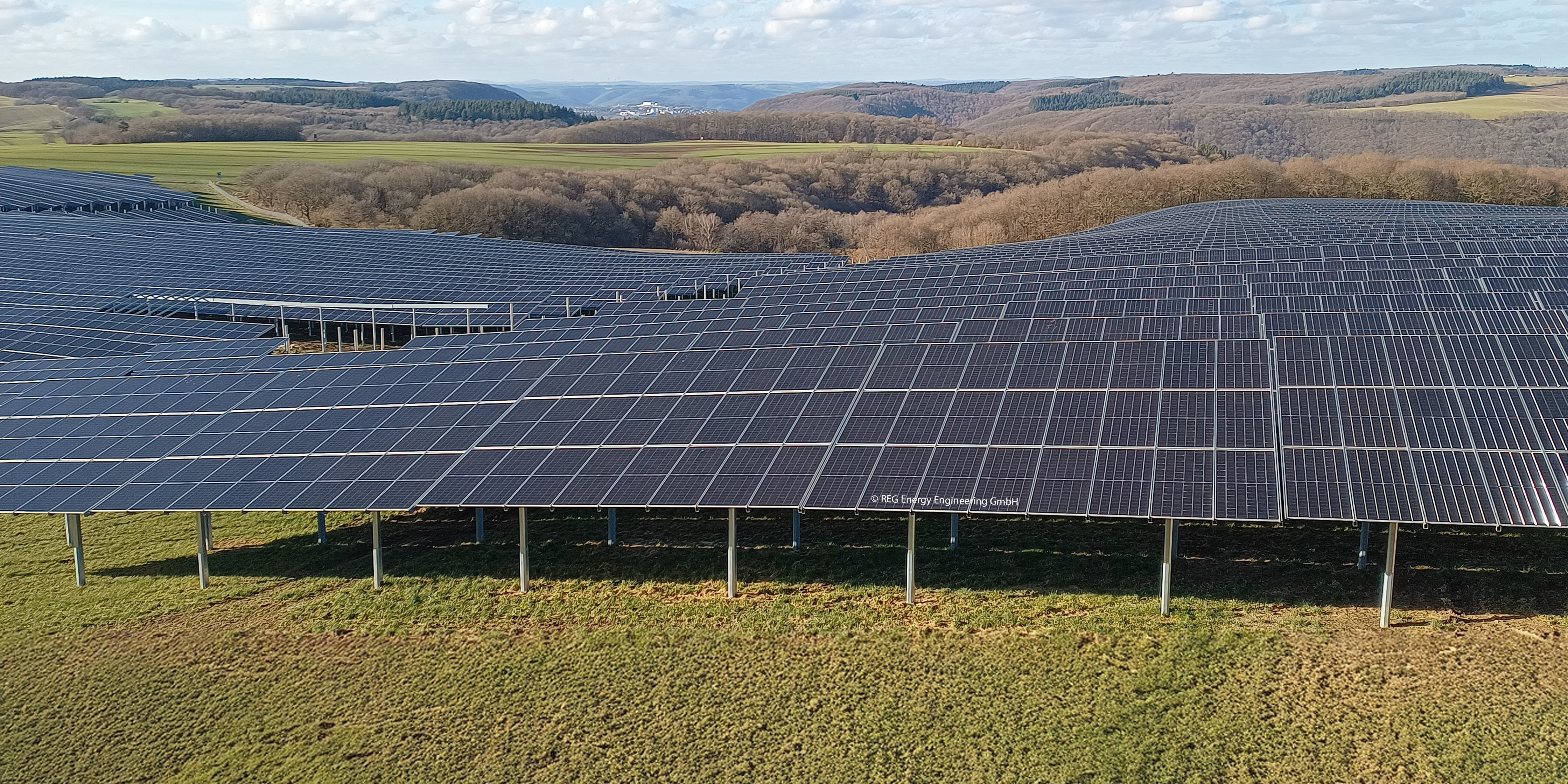
Agri-PV: Making Green Energy greener with Steel Substructures
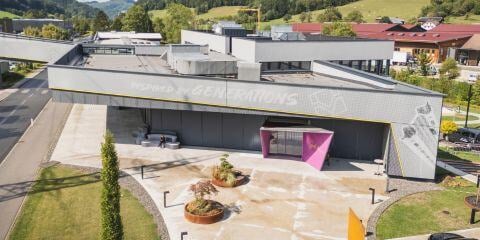
The Future of Steel in 2024: A Turning Point for the European Steel Industry
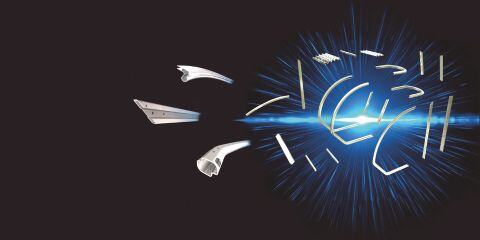