Mechanical Engineering: What does a sustainable Product Development Process look like ?
Sustainability is the topic on everyone's lips and is increasingly becoming a more central theme in both our private and professional environments. Be it Facebook postings from Fridays for Future, your own company’s sustainability report, heated TV discussions about climate change or revelations from your own family members who perhaps no longer want to fly or use coffee capsules in the future, the topic is on all our minds. Sustainability is also playing an increasingly important role in mechanical engineering. This goal can be achieved by, among other things, making sure that the machines are more durable, integrating several processing steps in one system, saving raw materials, observing the supply chain and, of course, by using more sustainable materials.
Ultimately, the product development process can not remain unaffected: the call for sustainable products is getting louder in all industries. It is sometimes, however, easier said than done. Material manufacturers, machine builders, plant manufacturers and processing industries are faced with problems that must be taken seriously. In this article we’ll pay special attention to the sustainable product development process and show challenges and solutions for the individual steps, using the roll forming process as our example.
Challenges in today’s Product Development Process
Depending on the individual requirements of each company, the product development process is designed differently and comes with different challenges. Nevertheless, we can address some overarching aspects:
- Time to Market:
With more new products coming onto the market faster and faster, your own product launch often has to be heavily promoted to consumers and buyers to stick out from the crowd. At the same time, competitors from all over the world are pushing their way onto the market with new developments and creating even heavier competition. Many decision-makers consider it important to shorten the time to market, and this impacts product development departments relatively quickly, where it has to be reconciled with factors such as tight budgets and a lack of human resources. - Cost Pressure:
As some of our higher/superiors love to repeat, the “fat years” are over. To stay competitive, more and more companies need to encourage their product developers to find cost-effective solutions - be it through the use of new technologies, inexpensive materials or automated process and production steps. - Lightening the Load:
With leaner designs, product developers can save weight and, consequently, material. As a result, process steps and further processing can often be simplified, so that further sustainable and cost-efficient advantages arise along the value chain. However, in order to be able to promote innovative and creative solutions, those responsible need the necessary background knowledge - for example, about alternative manufacturing methods and their potential, new materials, and other ways of saving weight. - Carbon Footprint:
Sustainable companies pay attention to the CO2 footprint of their products. This measures the amount of greenhouse gases that are released due to certain activities or processes. Here, too, product developers are under a certain pressure to develop sustainable products with a reduced carbon footprint. - Innovation Pressure:
The ever-increasing speed of technological developments from both home and abroad increase the pressure on product developers to innovate. Driving innovation topics forward in the company while at the same time protecting internal company secrets becomes a challenging balancing act - because progress can’t only take place at your own desk. Joint developments with partners who have expertise and technical know-how in specialist areas are also a key component of effective innovation. - Digitalization:
Digitalization and digital transformation are among the major trends of the 21st century, but they also come with challenges for organizations and users. The introduction of a new tool tends to come with a high cost of both time and money - so the question arises: which software is implemented in the company's own structures and which digital solutions are used by external stakeholders. - Raw Material Savings:
Producing sustainably often also means saving raw materials. Not only because of a climate-neutral approach, but also to reduce the possibly high material consumption and the associated costs.
The sustainable Product Development Process in 6 Steps, using a roll formed Section
Each product development process is unique, but generally tends to follow a certain structure. As an expert in roll forming, I’ll be using roll forming technology as the example process here.
Step 1: Requirements
At the beginning of the product development process, it’s a matter of defining the requirements for the new profile design and developing a rough idea. Since metal sections are generally semi-finished products, the sales engineers take a look at where the section is installed in the overall assembly and whether a perforation, thread or similar can be added.
It makes perfect sense to contact your metal section expert during the “requirements” phase in order to discuss initial design proposals and possibly get new input. Imagine, for example, a multi-chamber profile that, according to the first draft, is to be welded together from two square tubes. The resulting double material thickness could easily be saved with roll forming which not only saves weight, but also simplifies subsequent process steps in further processing.
Step 2: Project Planning
The second step is the project planning with the finished sketches, on the basis of which the design is examined by specialists. You can also create a cost overview in this phase - considering this early on in the overall product development process will help you find the most cost-efficient solutions. You can then directly submit a suitable offer.
Here, too, it’s a good time to talk with specialists you trust. With their shared years of experience dealing with similar requirements, they can quickly develop solutions that sometimes save material, weight and costs in the production of your metal section. For example, a roll forming specialist will be able to tell you straight away that steel profiles produced in larger quantities are even cheaper than aluminum profiles.
Step 3: Concept Creation
When creating the concept, the metal section is carefully examined and, if necessary, material tests are carried out. More complex profiles can be optimally simulated in the course of the feasibility check with software developed for this purpose. This 3D simulation as well as all tests and evaluations carried out serve as a reliable basis for the subsequent ordering and production process.
As a rule, a processing company is always at the cutting edge of technology with special methods, sometimes even defining the state of the art: with thickness optimization or the smallest radii for roll profiles, for example. Additionally, with regard to the products of their own sales partners, they should know about, e.g.: particularly wear-resistant or ultra-high-strength materials from local and, if required, global steel suppliers from all over the world.
Step 4: Prototype
Product developers like to have prototypes of metal sections that are required in mechanical or plant engineering produced manually at a machine shop, or with the help of a 3D printer. In the case of profiles, for example, a plastic model can easily be 3D printed to test whether it corresponds in appearance, shape, tolerance or function. At the customer's request, it is possible to produce a pilot series on the system, but this extra step is associated with extra costs - at least with roll forming, since only the original tools are used.
Simulations and prototypes of complex metal sections should always be discussed and thought through in a team, because different specialists combine a high degree of background knowledge and several perspectives. For example: new materials keep coming onto the market, but maybe only a few specialists will know about them, and many have not yet been tested.
Step 5: Optimization
The optimization step is a kind of extra fail-safe step only used when necessary. Roll-formed custom profiles, for example, can already be optimally prepared and designed for production with the help of simulations, so that subsequent optimization is no longer absolutely necessary. Nevertheless, it can often happen that something needs a last minute adjustment to perfect it.
Depending on the manufacturing method, this process step can be more or less flexible. If, for example, all tools are manufactured in-house for roll forming, it’s still possible to react quickly to last minute design changes, sometimes even on the system.
Step 6: Documentation
In ISO-certified companies (ISO 9001 or IATF 16949), the regulatory documentation in the product development process is clearly controlled and standardized. This includes, for example, machine data sheets where all process parameters are described and documented so that they can also be used for subsequent productions.
Conclusion: Sustainable Product Development Process in 2024
The topic of sustainability has reached almost all industries and departments. Sustainable product development along the entire value chain presents those responsible in mechanical engineering with diverse challenges such as time to market, reduction of weight and raw materials as well as digital and technological innovations. Since the best solutions are mostly found in a team and in exchange with experts, it’s worth getting your partners on board at an early stage. This way, you’ll be able to best exploit potential optimization options for materials, costs and processes.
Read more
Similar articles
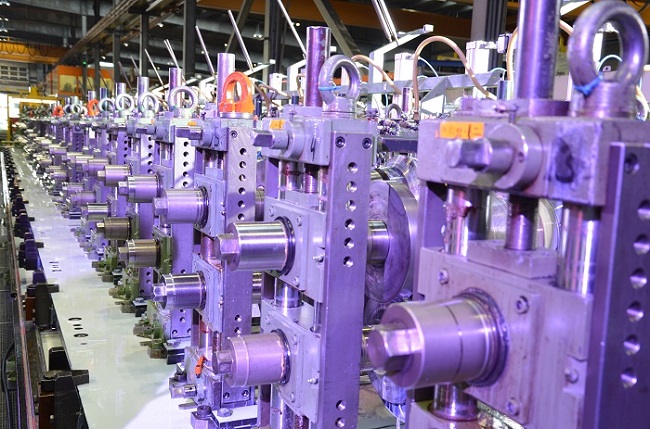
What is Roll Forming, and what can it do for you?
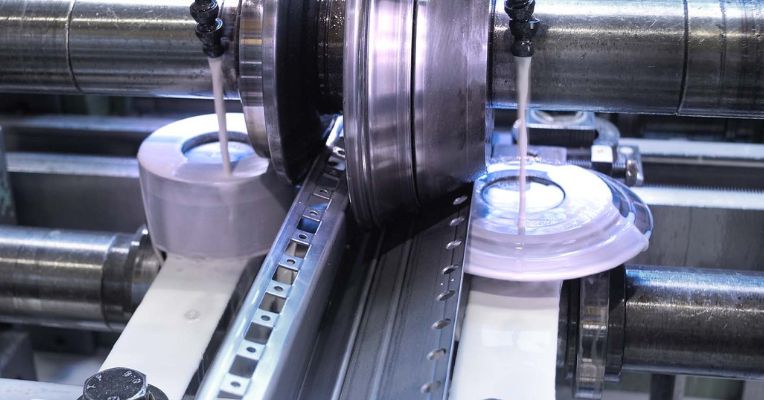
Do we still need Physical Prototypes in the Digital Age?
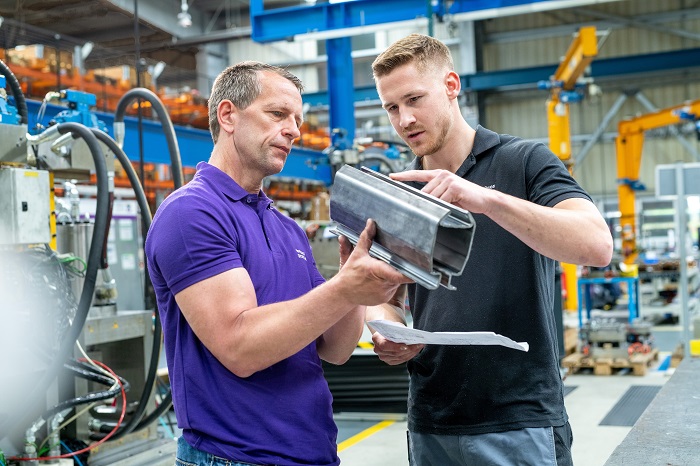