5 Important Technology Trends for Automated Storage and Retrieval Systems
Smooth-functioning warehouse technology is a key competitive factor in today's business world. It increases the overall efficiency of storage systems through optimized material flow and faster response times, and it significantly reduces the costs of internal company logistics. However, companies can’t just rest on the laurels of their previous successes in optimization measures for too long. Developments in warehouse technology are progressing rapidly, and with them, the potential for improvement in the business-critical realm of warehouse operations.
In this blog post, I’d like to introduce you to the five most important trends in automated warehouse technology. We’ll also look at why modern and efficient warehousing would hardly be possible without steel profiles. But first things first. Let's first get an overview of how automated warehouse systems are key to a company’s success.
What are Automated Storage and Retrieval Systems?
Automated Storage and Retrieval Systems - also known as ASRS - are technological solutions to improve the storage and management of goods in warehouses or other special storage areas. They use a variety of sophisticated tools, including robots, conveyor belts, shelving systems and specially developed software. By integrating these elements, the transport, storage and management of goods is made significantly more efficient. This automation not only saves time, but also improves accuracy and efficiency in all aspects of warehouse logistics.
In addition to the automatic storage and removal of various goods, shelf handling and inventory management are among the most important functions of an ASRS. The former enables space-saving and efficient storage of goods by utilizing and controlling different levels. Inventory management, on the other hand, is characterized by modern systems that document the entire warehouse inventory seamlessly and in real time.
Last but not least, the automatic transport of various goods between storage areas or to a specific picking area is playing an increasingly important role. And this is where our look into the future of automated warehouse systems begins.
The 5 most important technology trends in automated storage and retrieval systems
Innovative technologies are the most important basis for the continuous optimization of warehousing processes. Those who take advantage of the opportunities associated with these technologies in a timely manner will prevail in the market in the long term. In this section, I would therefore like to introduce you to the 5 most important technology trends in automated warehouse systems.
Technology Trend #1: Robotics and automation
More and more warehouse operations are relying on the integration of robots and automated vehicles to optimize their workflows. These robots play a crucial role in the picking, transport and placement of goods. They help to make the flow of goods more efficient and, as a result, improve the overall performance of the warehouse.
Technology Trend #2: Artificial Intelligence (AI) and machine learning
Thanks to the rapid development of artificial intelligence and machine learning, automated warehouse systems are becoming smarter at an impressive pace. They enable predictive analyses, detect errors, optimize storage strategies and adapt flexibly to changing requirements.
Technology trend #3: The Internet of Things (IoT)
In warehouse environments, IoT sensors are used to continuously collect real-time data on inventory, storage conditions and performance. This data makes it possible to optimize processes, manage inventory efficiently and predict maintenance needs. This allows warehouse operations to better control their operations and proactively respond to potential problems.
Technology Trend #4: Automated Warehouse Management Systems (WMS)
Modern WMS (Warehouse Management Systems) are equipped with advanced features, including real-time inventory tracking, order management, route optimization and storage location optimization. These features enable more efficient use of warehouse space and resources, resulting in improved workflows and optimized warehouse management.
Technology Trend #5: Augmented Reality (AR)
Augmented Reality (AR) is increasingly being used to optimize picking processes. By displaying digital information over real objects, errors can be reduced and the speed and accuracy of picking can be increased. This technology allows employees to access visual cues and instructions. This results in more efficient workflows and ultimately an increase in productivity in the warehouse.
As we can see, new technologies offer numerous opportunities for optimizing storage systems. However, these can only be used profitably if we get the basics right. This particularly applies to the frame structure of the whole storage system. The steel profiles installed here play a crucial role, as you will see.
The Key Role of Steel Profiles in Automated Storage Systems
Steel profiles form the strong backbone of automated storage systems and are crucial for smooth operation. Typically used in frame structures and support systems, they provide a robust base to support heavy loads and ensure the structural integrity of the entire storage system.
In addition, high-quality and precise steel profiles are often used in the construction of rails and guide systems that enable fast and precise movement control of the robots. This optimizes processes and increases productivity.
Although the innovative technologies of modern storage systems quite rightly inspire every optimization enthusiast, the steel profiles required for them are the secret star in the background. They are the indispensable component for the performance and efficiency of every automated storage system. Selecting the right provider is of crucial importance.
The 3 most important requirements for manufacturers of steel profiles for ASRS
Companies have to make a variety of decisions to realize the best possible solution for their specific storage technology requirements. This includes choosing a manufacturer and supplier for their steel profiles. Below you will find the 3 most important requirements that a manufacturer of steel profiles for automated storage and retrieval systems should meet:
- Just-in-Sequence-Deliveries
In contrast to many other areas of application, where companies usually require a complex design of a steel profile, storage technology requires rather simple cross-sections, but in many different designs. So a good supplier has to be able to provide different lengths, hole patterns and construction stages in exactly the order required on site, and all within the framework of smooth logistics. A simultaneous delivery of thousands of profiles would be completely impractical due to space constraints, and a delay in delivery of urgently needed parts would be extremely costly due to the resulting idle times. - Manufacturing to tight tolerances
Self-driving transport shuttles move at speeds of up to five meters per second. The rails for the underlying storage systems therefore require extremely tight tolerances. Even the smallest deviations accumulate from rail to rail and render the entire system unusable. Accordingly, a supplier is needed whose production facilities and processes are designed in such a way that they can reliably guarantee profiles with the required tolerances. - Processing of high-strength materials
Storage systems can consist of several thousand tons of steel profiles, which weigh a lot. By using higher-strength steels, however, profiles can be manufactured with less material while maintaining the same load-bearing capacity. In the end, this results in a huge potential saving of several tons of material and consequently significantly less budget expenditure for the construction of the storage system.
Given these diverse requirements, it quickly becomes clear that working with a traditional steel dealer is unlikely to produce optimal results. Rollformers, on the other hand, can make full use of their strengths. Let's now look at how they manage to do this.
Suitable Steel Profiles for Storage Technology: The Roll Profiler as the Perfect Source
A roll former offers a number of unbeatable advantages as a source of steel profiles in storage technology. Firstly, it can produce tailor-made profiles in large quantities and thus flexibly meet the specific requirements of a wide range of storage technology systems. This flexibility means that customers can receive profiles in different sizes, shapes and material thicknesses to meet their exact needs.
Secondly, the precision and consistency of roll forming ensures the high quality and reliability of steel profiles that is crucial for the stable construction of storage facilities.
And thirdly, by working with a roll former, companies can be sure that they will receive high-quality products that meet the high standards of modern warehouse technology systems. The efficient production method with minimal material waste also ensures maximum cost and time efficiency. So it’s not just good for your budget, but also for the environment.
Increase your efficiency with special profiles
While designers and product developers have long sworn by special profiles in many other areas of application, these flexible all-rounders have been used surprisingly rarely in warehouse technology. The reason for this lies in the widespread misconception that the development work would be too complex and too expensive. However, when all the circumstances are taken into account more closely, roll-formed special profiles are often economically superior.
An Example:
For one of our customers, we achieved a weight reduction of more than 30 percent thanks to a well-planned special profile. With a material requirement of several million linear meters per year, the associated advantages are clear:
- The significantly lower use of materials has enabled a significant reduction in unit costs.
- When loading and transporting the profiles, logistical advantages could be achieved due to the lower weight creating some indirect further cost savings.
- The lighter profiles with customized functions (holes, cross-sectional geometries, tabs) were easier to handle in manual assembly, which meant that time and personnel resources were used much more efficiently.
Before you categorically rule out a special profile for your storage system for supposed cost reasons, it’s better to play it safe and ask our experts. This approach is usually very popular among those in charge of budgets ;)
Conclusion: You can’t have an efficient storage system without a suitable substructure
By integrating advanced developments such as robotics, AI, IoT, WMS and AR, warehouse processes are significantly improved. Forward-looking companies are finding unprecedented opportunities to optimize their warehousing, reduce costs and increase customer satisfaction. Those who invest in the right technologies in good time will prevail in an increasingly competitive market.
But you can’t forget about the basics. Without high-quality and precisely fitting steel profiles, the technologies for automated storage systems can’t function efficiently. As a roll profiler with many years of experience with complex storage technology, we’ll happily support you in the design and implementation of a tailor-made solution that also meets your requirements for reliable just-in-sequence processing. Simply contact our experts. Together we can build the best automated storage system for your business.
Read more
Similar articles
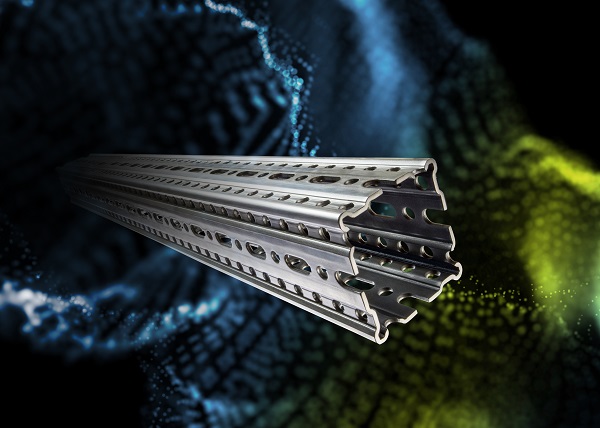
Mechanical Engineering: What does a sustainable Product Development Process look like ?
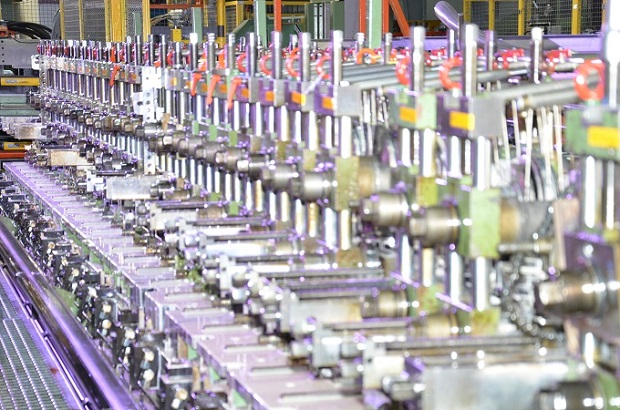
Steel doesn’t grow on Trees? How to deal with Raw Material Scarcity
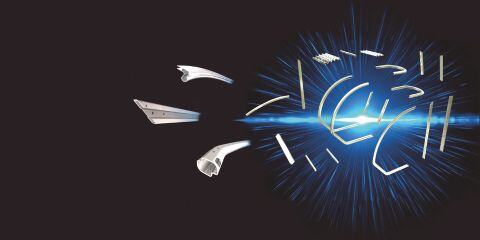